Technical Library
- HOME
- Technical Library
- FPD Equipment | Optimizing Etching with High-Precision, Uniform, Responsive Slit Nozzles
FPD Equipment | Optimizing Etching with High-Precision, Uniform, Responsive Slit Nozzles
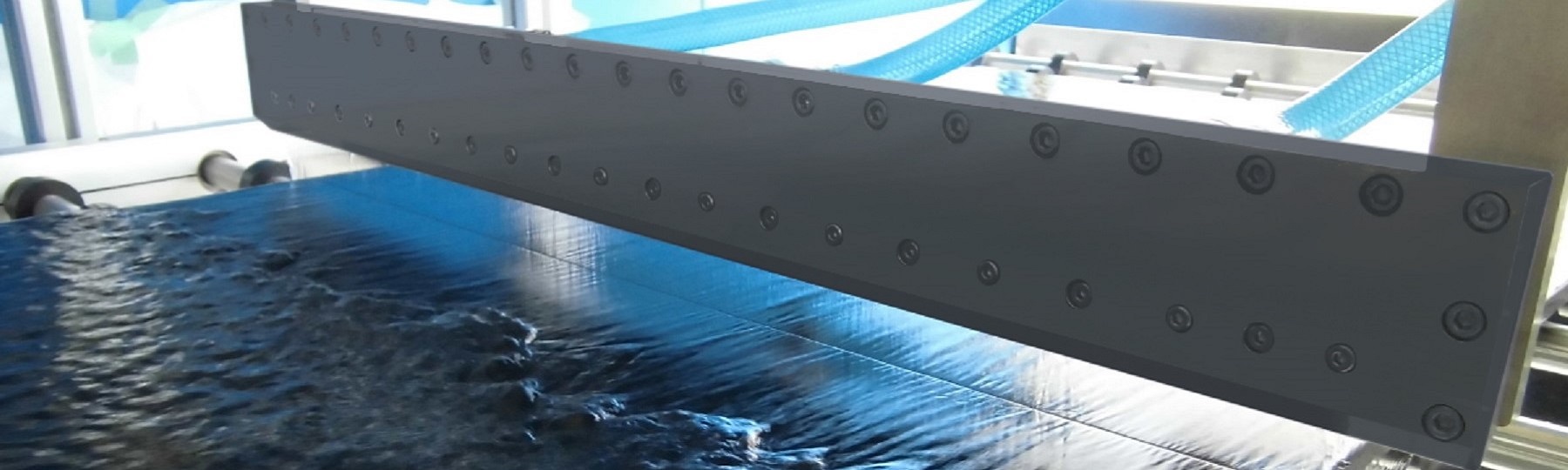
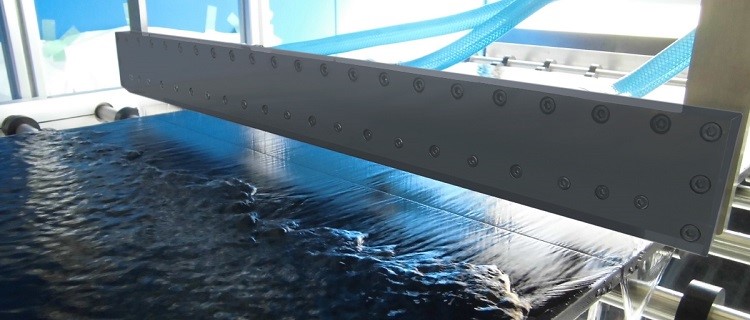
Solutions or Products Featured in This Case Study
- High-Precision, Low-Flow, and Responsive PVC Slit Nozzles | SLHN-K Series
Key Reasons for Implementation
- Developed a product that fully meets all stringent requirements.
- Presented a prototype nozzle spray video, effectively easing customer concerns.
- Achieved a competitive cost while maintaining high performance.
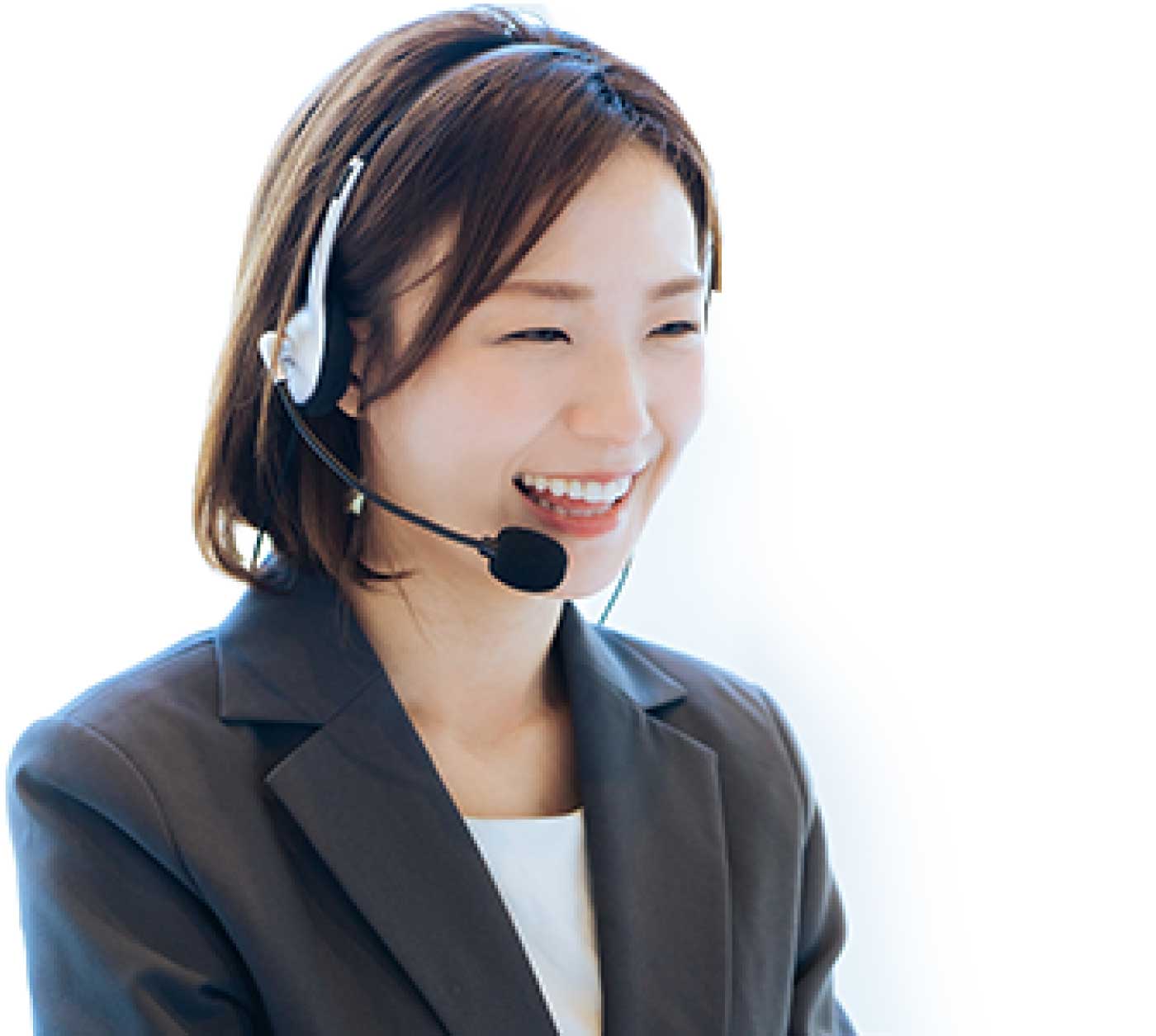
- Not sure which product is right for you?
- Curious about the total cost?
- Wondering where to start?
- We’re here to help – reach out with any questions.
Challenges Faced by the Customer
A flat panel display (FPD) equipment manufacturer was working to enhance the performance of slit nozzles for their next-generation model. Slit nozzles, also known as water knives or aqua knives, discharge purified water or chemical solutions in the form of a thin liquid film onto workpieces.
The requirements for this nozzle were as follows:
- Chemical resistance: Must be made of materials that can withstand etching solutions.
- Uniform liquid film formation: Stability is essential as it directly impacts product quality.
- Low flow rate: Enables savings on expensive etching solutions.
- Excellent responsiveness: Must allow rapid on/off control of liquid film discharge.
- Drip prevention: No liquid should drip after spraying stops.
These requirements were highly demanding and exceeded the performance capabilities of existing nozzles by a significant margin.
Proposals from IKEUCHI
The requirements presented by the customer were exceptionally challenging. However, we committed to developing, designing, and manufacturing a slit nozzle that meets all the performance criteria, including chemical resistance, stable and uniform liquid film formation, low flow rate, high responsiveness with on/off control, and drip prevention.
To drive the project forward, a dedicated team was formed, comprising the customer’s development engineer, our sales representative, and the chief design manager from our factory. Starting from scratch, we conducted multiple rounds of design and prototyping, presenting spray demonstration videos of each prototype nozzle to the customer to systematically resolve their concerns.
As a result, we successfully developed a slit nozzle that met all the requirements, and the delivery of mass-produced units has finally begun.
Benefits Achieved
The design of a new flat panel manufacturing equipment model, featuring high-performance slit nozzles that apply etching solutions with precision and uniform liquid film thickness, has been successfully completed. These nozzles optimize the etching process and significantly reduce the consumption of expensive solutions, resulting in a more efficient piece of equipment.
This equipment is now being deployed in FPD production facilities across various Asian countries, playing a vital role at the forefront of precision flat panel manufacturing.