Industrial Cooling Business
These systems utilize latent and sensible heat properties
to maximize cooling efficiency
for all cooling objects.
Our proposals are visualized in a 3D simulation using computational fluid dynamics (CFD) and spray pattern modeling.
We strive to make sure you have an understanding of the benefits based on the results of the cooling experiments before proceeding with installation.
Maximizing the capabilities of water
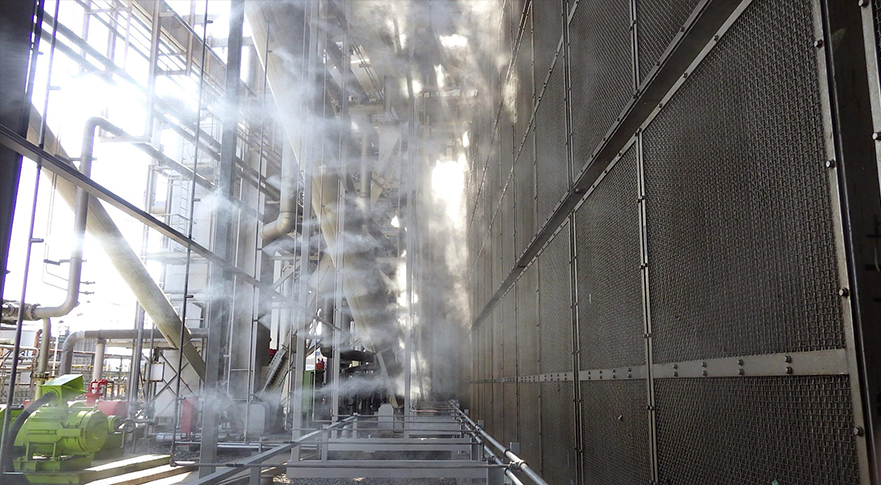
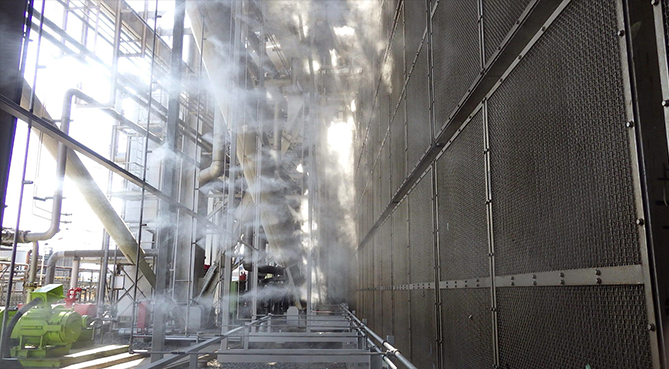
IKEUCHI’s cooling systems maximize the capabilities of water. Although water is a ubiquitous resource, it has the greatest latent heat potential compared to other substances. We excel at precisely controlling a variety of parameters such as cooling speed and range by utilizing both the sensible and latent heat properties.
In the industrial world, the cooling process has been viewed lightly as a post-process that generally follows industrial heating processes. It is important to understand, however, that industrial cooling has enormous potential. It is a known fact that users can enjoy a broad variety of benefits, including improved product quality and mitigation of energy-related and environmental problems.
For example, the method used to cool iron can be either rapid or slow, but the cooling method results in iron with completely different properties. When dealing with flue gases, measures such as finding an optimal balance between cooling and heat recovery, and making efficiency improvements to hazardous substance removal operations can optimize the size of gas treatment equipment, which occupies a large space in a plant, while also boosting its efficiency.
Furthermore, looking back on our consulting service operations, we have always engaged in repeated, in-depth discussions with each customer, even customers in fields that do not devote much attention to cooling-related operations, and through these efforts we were able to discover a great number of underlying customer needs. We believe it is IKEUCHI’s role to uncover customer needs and provide high-quality services.
Because cooling conditions vary greatly in terms of target cooling objects, worksite conditions, and other factors, applying an approach that was successful with one customer may not be effective at another customer’s case. It is necessary to optimize each cooling system for each different project. Consulting services, which serve as the core of the cooling business, involve meetings between highly experienced IKEUCHI specialists and the customer in order to discern customer requirements and worksite conditions in detail, and discussions for us to propose an optimal solution.
Cooling experiments and simulations
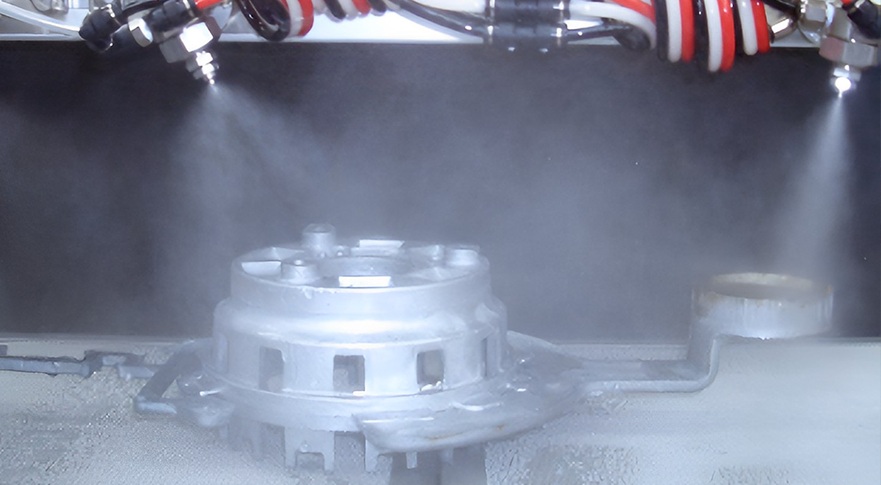
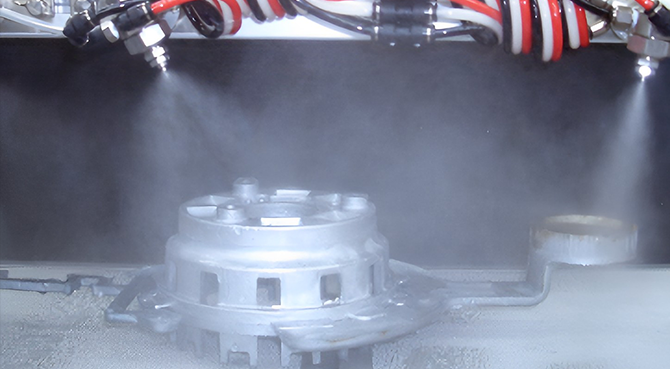
At that time, we place particularly strong emphasis on cooling experiments and simulations.
By presenting the contents of our proposal in a visualized form with the experiments and simulations, we hope to convey concrete images of the benefits together with the introduction of the system.
Equipment for cooling experiments
We have two types of experimental equipment, those for solid-matter cooling and those for gas cooling.
Because no two cooling proposals will be the same, we conduct experiments using experimental equipment that can simulate a field in different conditions.
Simulations
We create 3D models of customer worksites using computational fluid dynamics (CFD) technology and use them to carry out comprehensive monitoring of cooling conditions and various other factors.
We start with modeling of nozzle atomization mechanism, which involves simulation of droplet diameters, spray patterns and so forth required for cooling. Then, we perform simulations for either gas cooling optimization or solid-matter cooling optimization depending on the objects to be cooled.
-
Modeling of nozzle atomization mechanism
Spray pattern modeling is very difficult because it depends on various conditions such as droplet size, droplet size distribution, density of droplets, initial velocity, and spray patterns.
However, conducting this simulation with high precision lays the foundations for success in building high-efficiency cooling systems.
Therefore, we conduct simulations such as airflow and temperature distribution with the greatest accuracy possible by using dedicated measuring instruments and computational fluid dynamics. -
Gas cooling optimization
A wide range of conditions must be considered when it comes to gas cooling.
Temperature conditions, for example, cover a wide range, from air at room temperatures to high-temperature exhaust gases.
Also, various types of gases are targeted for cooling: those in a steady state are characterized by calm, gradual volumetric and temperature changes, whereas unsteady-state gases may exhibit rapid shifts from zero to maximum gas volume levels in mere seconds.
In order to create a model that covers all of these cases, high-precision spray pattern modeling alone is not enough.
Engineers with real-life experience and keen sensibilities developed along the way are needed to run these simulations. -
Solid-matter cooling optimization
When it comes to solid-matter cooling operations, various types of objects are targeted, and in almost all cases unsteady-state modeling is required.
Microscopic-level examination is needed to analyze surface-level phenomena such as surface-adhering vaporization, rebound, redispersion, liquid film formation and so forth.
However, because many of the items targeted for cooling are large in size, macroscopic-level considerations are also necessary.
IKEUCHI was one of the first to focus on these phenomena and start pursuing relevant research.
Our engineers with a rich array of experience lead customers to optimal solutions.