Boosted Productivity in Notebook Manufacturing with Dry Fog Humidification
Technical Library
- HOME
- Technical Library
- Revolutionizing Direct Mail Printing with Dry Fog Humidification
Revolutionizing Direct Mail Printing with Dry Fog Humidification
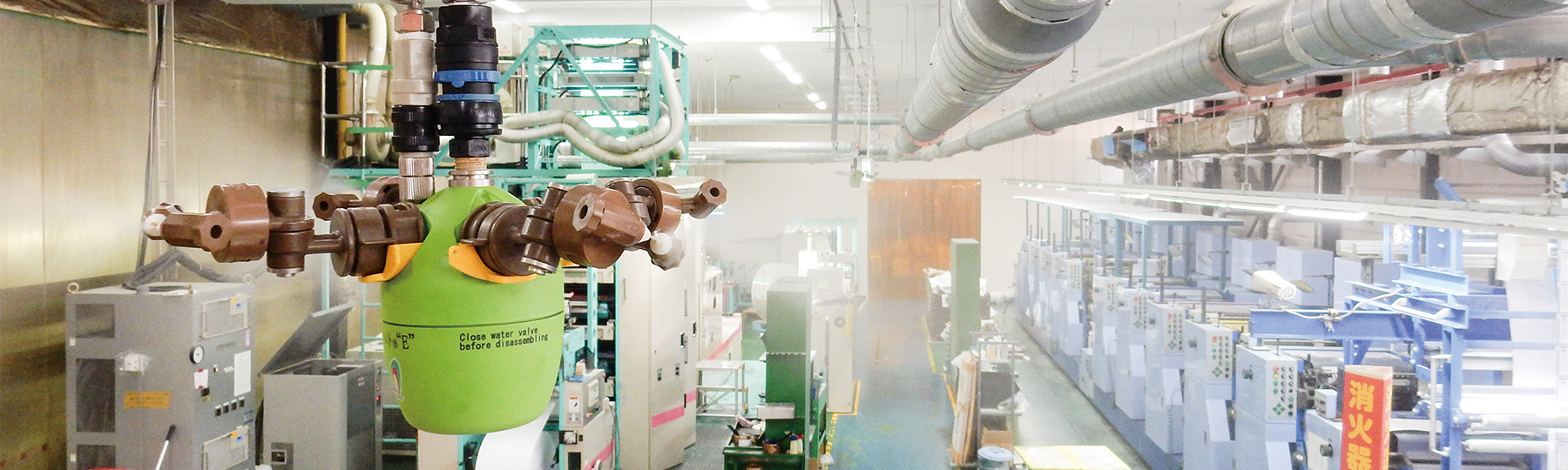
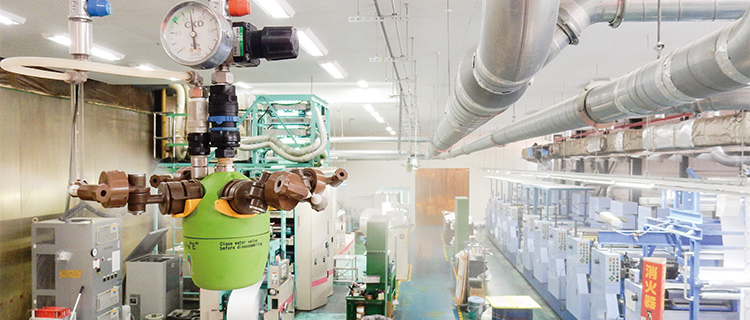
About KOHHOKU Printing Co., Ltd.
At KOHHOKU Printing Co., Ltd., a leading direct mail printing company for major correspondence education providers and e-commerce companies, innovation drives efficiency. The company has revolutionized its operations by automating intricate direct mail printing and sealing processes, enabling them to offer cost-effective services with rapid turnaround times.
Solutions or Products Featured
in This Case Study
Controlling Pitch: A Critical Element in Production
In the production of snap pack direct mailers, also known as pressure-sealed mailers, controlling the pitch between paper sheets in the initial printing process is critical and significantly affects the efficiency of subsequent processes. Poor humidity control can cause paper expansion or contraction, leading to pitch misalignment. In severe cases, this may necessitate a complete reprint.
A single occurrence of such failure not only results in financial losses ranging from $2,000 to $3,000, but it also significantly reduces productivity.
Paper expansion and contraction are highly delicate issues; even a 1mm deviation in a 100-inch pitch can lead to defects. Because our manufacturing processes are spread across different factory buildings, differing humidity levels have exacerbated the problem.
To address this challenge, we determined that optimizing humidity levels across all the factory buildings and printing processes was imperative. Leveraging our experience with the AirAKI® system, which had previously been installed in some buildings, we have extended its implementation to all facilities.
The Superiority of AirAKI®
Before and after the initial installation of the AirAKI®, we explored various humidification methods and systems from different manufacturers. However, despite frequent nozzle clogging, these systems failed to maintain the necessary humidity levels.
The AirAKI® system distinguishes itself with its virtually trouble-free operation and its capability to ensure consistent humidity levels without causing dampness, even over long maintenance intervals.
Moreover, the clean water supplied to the system from the water purifier does not damage electronic circuit boards and can also be utilized as dampening water in printing. The shift to controlling humidity based on absolute humidity levels, as you suggested, was a pivotal improvement. When we relied on relative humidity control only, we experienced equipment short-circuits due to condensation.
Enhancing Operational Efficiency and Reducing Defects
By combining the AirAKI® with dehumidifiers, we can now maintain stable humidity levels throughout all seasons, which significantly improves the misalignment problem caused by paper expansion and contraction. Additionally, using static eliminators alongside this system has drastically reduced machine stoppages due to static electricity at the sheet delivery section, resulting in an approximate 19% increase in operational efficiency.
Furthermore, we dispose of defective work-in-progress containing personal information by either shredding or melting. By reducing these defects, we have also significantly cut labor and disposal costs, thereby making the cost-effectiveness exceed the operating costs of the AirAKI®.
The greatest highlight has been the improvement in customer satisfaction, which stems from our enhanced productivity that now enables us to deliver complex direct mail processing exactly within the tight schedules we’ve planned.
Establishing Humidity-Controlled Environments
In addressing issues at a printing factory, it is crucial to first establish an environment that supports both the prevention of problems and the accurate diagnosis of failures by implementing effective humidity control across all factory buildings. Humidification is effective for more than just static electricity issues; furthermore, static electricity cannot be fully tackled with static eliminators alone.
First, we establish the controlled environment, including humidity and temperature, then address any localized issues. Reversing this sequence will lead to a series of makeshift, reactive measures.
“I firmly believe that implementing humidity control through the AirAKI® system was essential for sustained productivity enhancements.”
Dry Fog Humidification System, AirAKI®
Industrial Humidification System Using Non-wetting “Dry Fog”
The AirAKI® is an advanced industrial humidification system that generates “Dry Fog*” to create optimal humidity environments across diverse worksites.
The system significantly enhances productivity and improves yield rates by preventing problems caused by dryness and static electricity. Moreover, compared to steam humidification, it has excellent energy efficiency, with running costs being approximately one-fifth.
*We define “Dry Fog” as a fog with a mean droplet diameter of 10 μm or less.
Dry Fog Humidification System, AirAKI®