Technical Library
- HOME
- Technical Library
- Boosted Productivity in Notebook Manufacturing with Dry Fog Humidification
Boosted Productivity in Notebook Manufacturing with Dry Fog Humidification
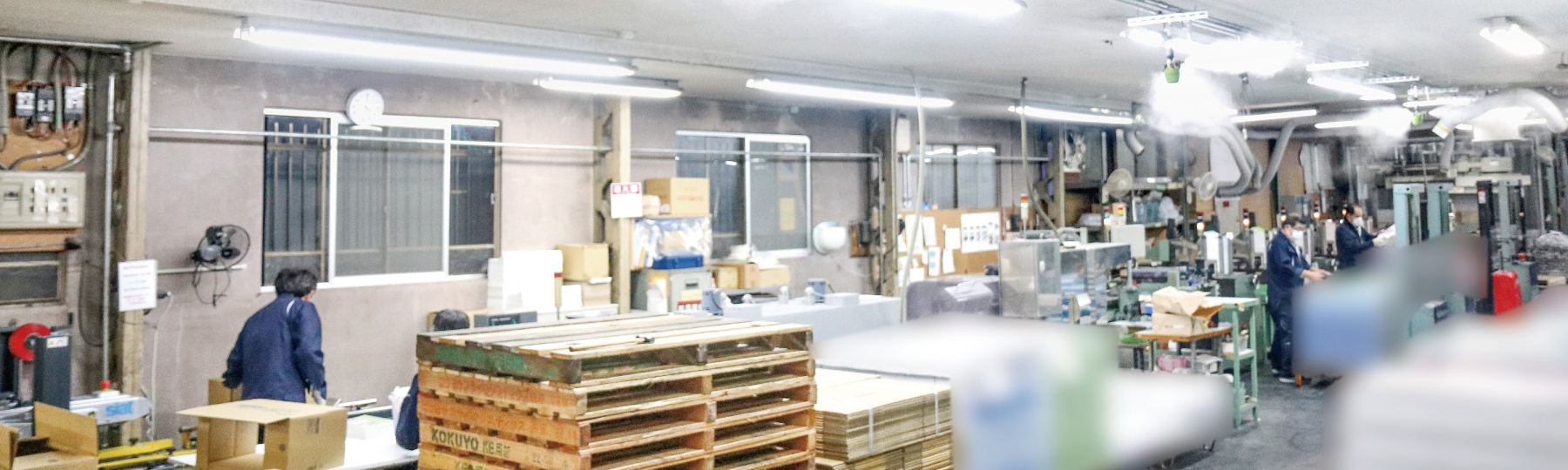
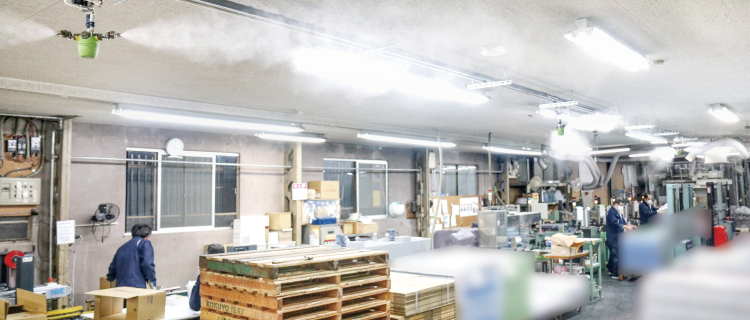
About OHGURI SHIKO Co., Ltd.
With more than 40 years of expertise in manufacturing bound notebooks, OHGURI SHIKO Co., Ltd. upholds the motto, "Let's create products we would want to buy ourselves." The company is dedicated to crafting notebooks whose quality is fully appreciated only through use, continually refining its production technology. Recently, OHGURI SHIKO has focused on the “Mahora” notebook, specifically designed to meet the needs of individuals with developmental disorders.
Voice of the Customer:
"We really can't imagine going back to a time without the 'Dry Fog Humidification System.' It has become something indispensable."
Solutions or Products Featured
in This Case Study
Bound notebooks
Decreased Productivity during the Winter Season
Mr. Takamitsu: When I first began leading the productivity improvement project, our factory didn’t have any industrial humidification systems. In winter, we faced a variety of problems seemingly caused by dryness.
Especially on the second floor, dedicated to producing mini-sized notebooks, the situation was severe. We faced challenges such as paper warping, sheets sticking together, and double feeding causing paper jams in the machines, leading to a noticeable decrease in productivity.
Mr. Ohguri: Compared to the productivity during periods of stable humidity, in winter, we observed a 40% decrease on the first floor, where we manufacture semi-B5-sized notebooks, and an approximately 60% on the second floor. It seems that the second floor, in particular, is susceptible to dry conditions. Despite trying commercial humidifiers and anti-static ropes, the situation did not improve.
Mr. Takamitsu: I simply didn’t want to propose an investment by hastily concluding that “the decrease in productivity is due to dry conditions.” During my interviews with the onsite operators, they mentioned, “In winter, dry paper rubs together, causing static electricity,” but we lacked quantifiable data to form a basis for investment decisions.
A Correlation between Humidity and Productivity
Mr. Takamitsu: So, I decided to measure the environmental data and productivity on the worksites and gather statistics. As expected, a clear correlation between humidity and decreased productivity emerged. With evidence highlighting the importance of humidity control and calculations estimating the investment recovery period through productivity improvement, we officially began considering the installation of a humidification system.
An Extensive Track Record in Printing Factories
Mr. Takamitsu: Our requirements for the humidification system were threefold: 1) reasonable running costs, 2) no adverse effects on paper or machinery, and 3) user-friendly with minimal operational complexities. We investigated various humidification methods, including steam-based options, but what best matched our requirements was IKEUCHI’s Dry Fog Humidification System.
IKEUCHI has an extensive track record of delivering this system to printing factories, which handle paper, much like ours. The system is capable of automatic operation with a direct connection to the water supply. The appeal also lies in the ease of maintenance, requiring only an annual replacement of filters of a water purifier. Additionally, there is an option for a comprehensive maintenance contract. The initial stages of the assessment process went very smoothly, and we were already leaning towards the adoption of Dry Fog Humidification system.
A Surge of Opposition Views
Mr. Takamitsu: However, there was substantial resistance among the operators towards Dry Fog Humidification, a system that directly sprays water. They argued, “Water spraying in a manufacturing environment is absurd,” “Paper will get wet,” and “Machines will rust.”
Mr. Ohguri: Onsite operators tend to resist substantial changes, especially when introduced to an unfamiliar humidification method involving water spraying. “Even if productivity improves, won’t the quality suffer?” It’s natural to have concerns about various risks, and there appears to have been strong resistance against him.
Mr. Takamitsu: Coming from a different industry and being in my third year, I understand the skepticism towards proposals from someone who doesn’t fully understand the onsite operations. Therefore, I decided to temporarily borrow a demo unit of the Dry Fog humidifier to allow the operators to verify the risks for themselves.
Verification with the Demo Unit Leading to a Shift in Opposite Views
Mr. Takamitsu: Upon the arrival of the demonstration unit, they extensively tested it by trying various actions, such as exposing paper to the fog and humidifying the process line where paper jams occurred, until everyone was convinced.
As a result, opinions shifted with comments like, “I thought the paper would definitely get wet with this much fog, but it stays dry,” and “This is impressive.” The evaluation reversed as not only did the paper stay dry, but also the occurrence of paper jams reduced, and they finally became convinced after experiencing the effectiveness.
Considering Additional Installation
Mr. Takamitsu: Without delay, I explained the payback period to the internal team, and we decided to expedite the installation on the second floor to meet the winter deadline.
Mr. Ohguri: As a behind-the-scenes story, at this time, I was actually considering whether to introduce it to the first floor as well. The reason is, on the first floor, there are several automatic inserters for sending a few notebooks together to the shrink-wrapping machine. However, during winter, the required number of operators for that process doubles.
Under normal circumstances, six operators are to manage the notebook insertion process while concurrently conducting quality checks. However, in winter, they have to manually straighten warps in the notebooks, but the machine still cannot automatically insert them, compelling them to do it manually. This manual insertion process requires a double number, totaling 12 operators, resulting in a 50% decrease in productivity in that process.
Mr. Takamitsu: Exactly. However, I suggested, “Let’s take a wait-and-see approach for now.” The first floor is more spacious than the second floor, and there’s a concern about humidity dispersing. Moreover, when considering the overall scenario, the decline in productivity is not as pronounced as on the second floor.
Although it’s evident that productivity increases with humidification, it appears that the payback period might be slightly longer on the first floor. So, I conclude, “Let’s observe the situation.”
A Green Light and Unexpected Outcome
Mr. Ohguri: However, I was aware that the first floor was also facing challenges, and since we had seen significant results on the second floor, I said, “Let’s go for it!” I gave the green light for the installation on the first floor myself (laughs).
Mr. Takamitsu: That was quite reliable (laughs). Following that, we installed it on the first floor, and the mentioned automatic inserter can now operate with just six operators even in the winter. It’s been a year since then, and I’ve come to realize that my thinking at the time was a bit too optimistic.
Typically, humidification is associated with autumn or winter. The installation of Dry Fog Humidification System was also focused solely on recovering productivity during dry periods.
Dry Fog Humidification System, AirAKI, in operation (2nd floor)
However, from the operators, we were asked, “Can we use this year-round?” This is because, even during periods other than winter, when humidity is relatively stable, there are actually fluctuations in humidity from day to day. Though the occurrences are infrequent, minor issues due to dryness were occurring throughout the year.
Surprisingly, by operating Dry Fog Humidification System year-round, even during the summer if necessary, we achieved a consistently stable humidity level throughout the year, and the effectiveness exceeded our initial calculations. Upon reevaluating, it became clear that the investment could be recouped in a much shorter period than initially estimated.
Additionally, even in areas we initially believed were beyond the effective range of humidification, such as slightly more distant locations, paper jams were reduced. It was truly surprising to witness such a significant impact from mere humidification, surpassing our expectations.
Dry Fog Humidification System, AirAKI, in operation (1st floor)
After the Introduction of Dry Fog Humidification System
Mr. Takamitsu: Being in charge of production control, this was my first assignment where the company made an investment, and I was really determined not to make any mistakes.
While there were various challenges during the introduction, we were able to achieve solid results, earning trust from the onsite operators.
Everyone seems to think, “If it’s Mr. Takamitsu, he’ll thoroughly research and introduce good products.” After this successful experience, I’ve felt that my work has become much easier.
In that sense, it’s a humidification system that has improved not only the productivity on the site but also my productivity afterward (laughs).