[PDF] Dry Fog Humidification Solutions for Printing: 8 Case Studies
Technical Library
- HOME
- Technical Library
- Dry Fog Air Conditioning to Boost Output by 30% and Improve Quality in Textile Factories
Dry Fog Air Conditioning to Boost Output by 30% and Improve Quality in Textile Factories
- Textile
- Industrial Humidification
- AirAKI
- AKIMist
- Weaving
- Moisture Conditioning
- Air Conditioning
- Cotton Fabric
- Yarn Breakage
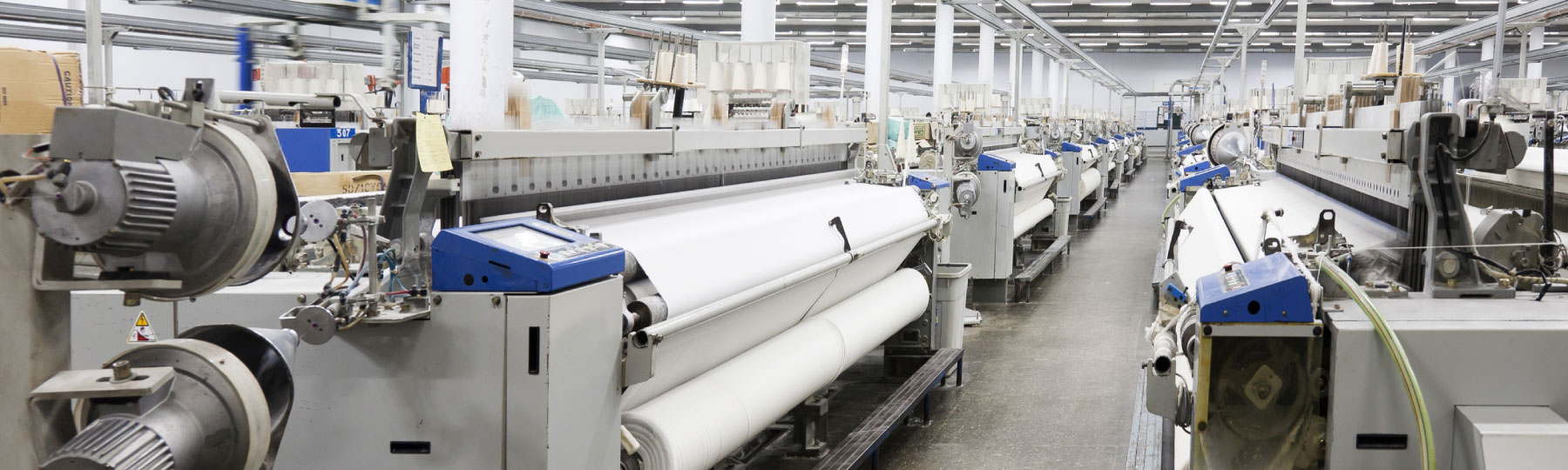
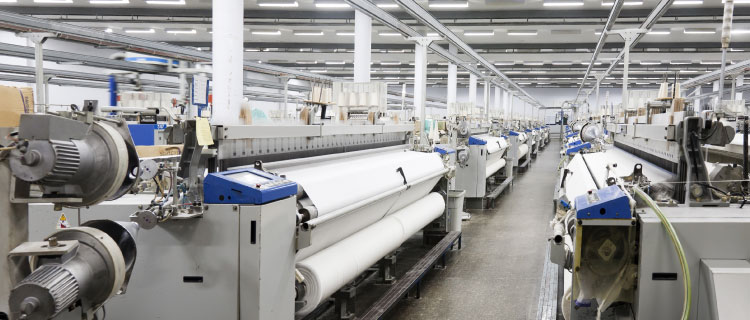
Solutions or Products Featured
in This Case Study
Key Reasons for Implementation
- Proven Effectiveness: On-site Dry Fog spray tests confirmed the system’s effectiveness.
- Cost-Effective Solution: The system improved air conditioning by retrofitting existing equipment, avoiding the need for expensive HVAC upgrades.
- Flexible Installation: Its highly adaptable layout enabled phased implementation, starting with high-priority zones.
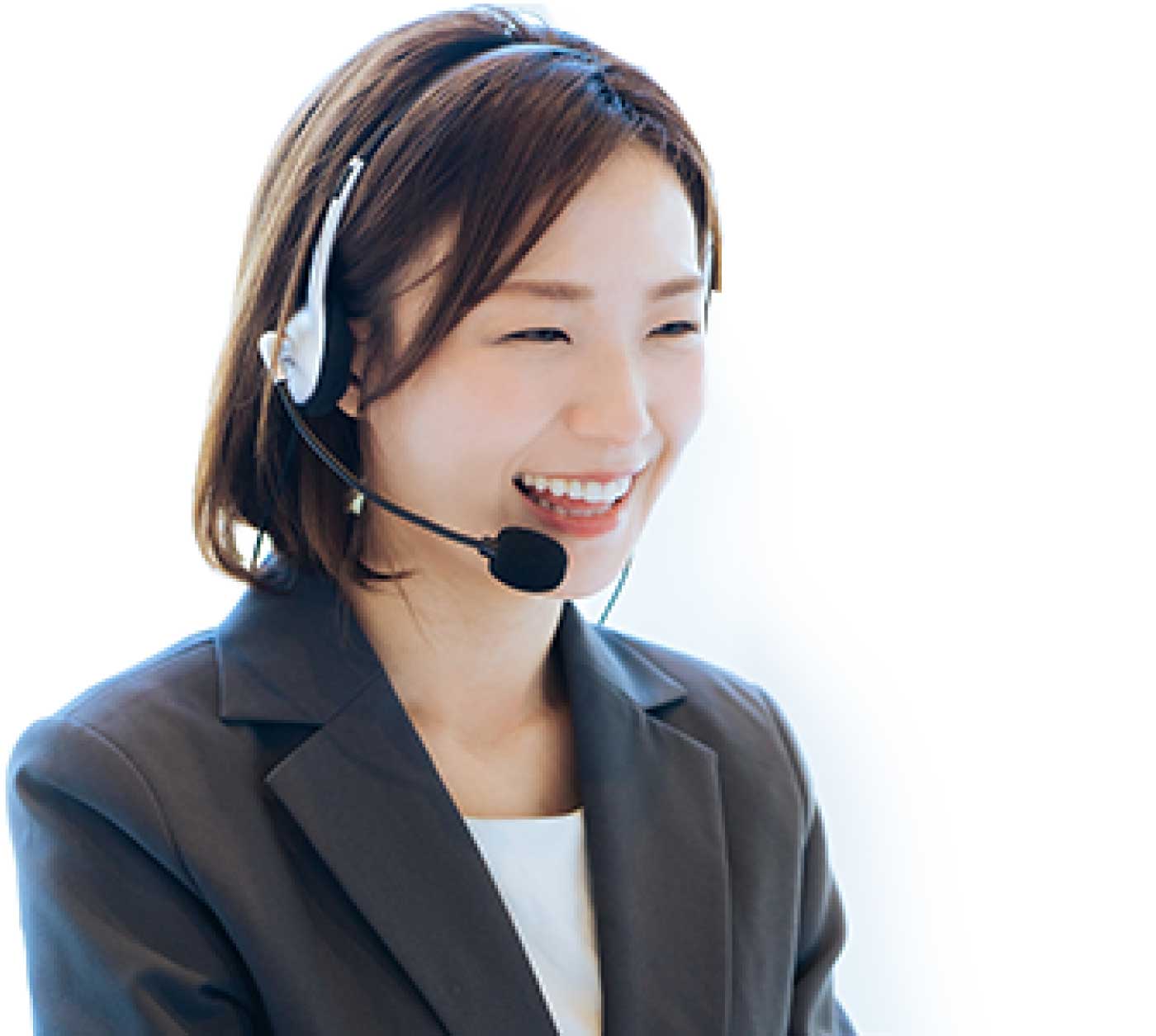
- Not sure which product is right for you?
- Curious about the total cost?
- Wondering where to start?
- We’re here to help – reach out with any questions.
Challenges Faced by the Customer
At a cotton weaving factory in Indonesia, the customer faced a significant challenge: productivity in the weaving process declined during the hot daytime hours.
Expanding the factory floor and installing numerous additional air-jet looms strained the capacity of the existing air conditioning system.
In the weaving process, especially when using cotton yarn, precise temperature and humidity control is essential for maintaining high product quality. To address this challenge, the factory resorted to air conditioning only half of the production floor.
However, in the non-air-conditioned areas, room temperatures rose as high as 35°C, frequently triggering thermal switches on the looms and causing machines to stop unexpectedly.
Each time a machine stopped, operators were required to inspect the quality of the work-in-progress, reset the weft yarn, and restart the operation, which placed a significant burden on them. Additionally, out of concern for further stoppages, the looms were operated at reduced speeds, inevitably leading to lower productivity.
The factory considered upgrading its air conditioning system, but the estimated cost of $300,000 made it difficult to justify the investment. As the thermal switches were set to activate at 32°C, it was essential to find a way to keep the room temperature below this threshold. Amid these challenges, the factory reached out to IKEUCHI for a solution, following a recommendation from a nearby spinning factory.
Proposals from IKEUCHI
IKEUCHI proposed installing the Dry Fog humidification system, AirAKI. This system lowers room temperature through the evaporative cooling effect of its ultra-fine fog, Dry Fog, while maintaining optimal humidity levels with automated operation. Additionally, it prevents thread breakage caused by dryness and helps preserve fabric quality by maintaining appropriate moisture content in the cotton.
In addition, IKEUCHI proposed dividing the floor into separate zones and using vinyl curtains to prevent the Dry Fog from dispersing. This approach made it possible to implement the system gradually, starting with high-priority zones.
Benefits Achieved
- Room temperature dropped by 4°C to 31°C, significantly reducing loom stoppages and production interruptions.
- Loom operating speeds increased, resulting in a 30% boost in production output.
- Stable humidity levels eliminated thread breakage and other related problems.
- Airborne cotton dust levels were effectively reduced.
- Most importantly, the 4°C temperature reduction improved working conditions for employees, leading to positive feedback from the workforce.