Technical Library
- HOME
- Technical Library
- Humidification Solutions for Reducing CO2 Emissions at a Semiconductor Plant
Humidification Solutions for Reducing CO2 Emissions at a Semiconductor Plant
- AirAKI
- AKIMist
- Industrial Humidification
- Energy Savings
- Semiconductors
- SDGs
- Carbon Neutrality
- CO2 Emissions
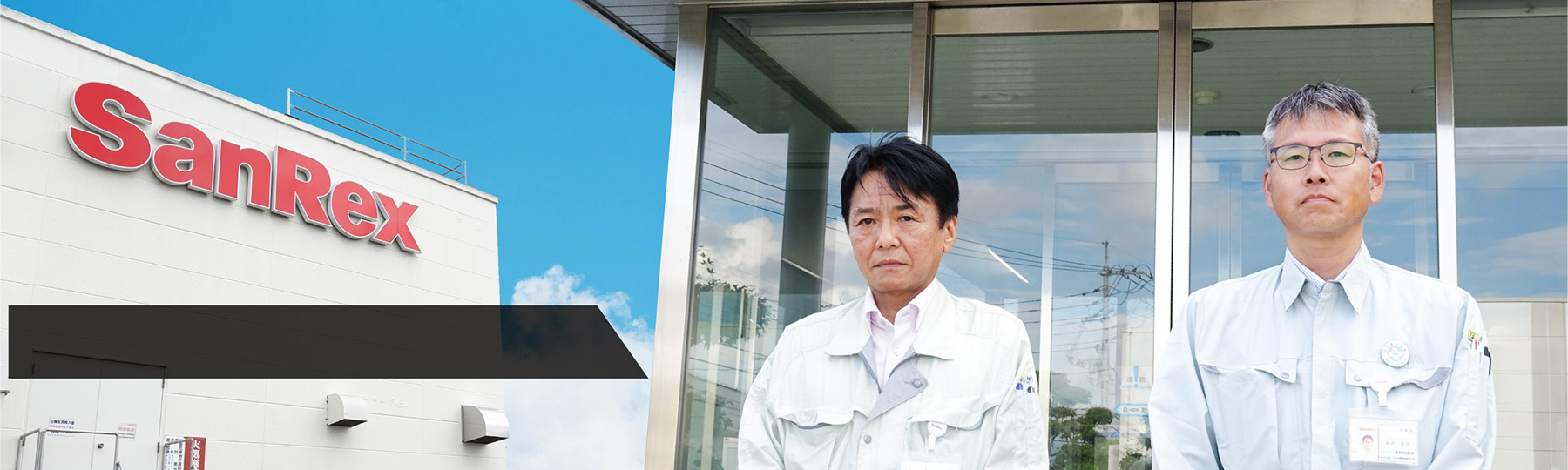
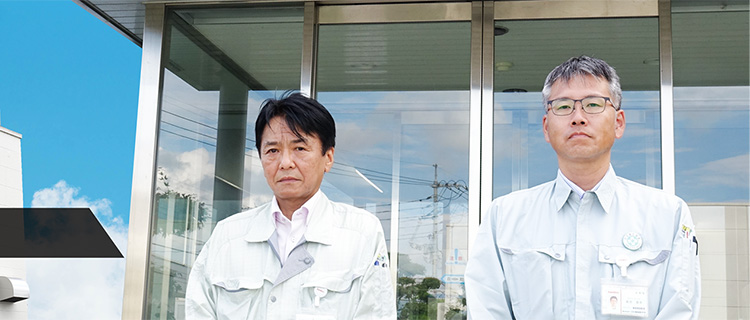
About SANSHA ELECTRIC MANUFACTURING CO., LTD.
SANSHA ELECTRIC MANUFACTURING CO., LTD., which manufactures power semiconductors at its Okayama Plant, has achieved significant energy savings in its energy-intensive cleanroom processes. Consequently, the company has received the 38th "Excellence in Energy Saving Equipment Award" from the Japan Association of Refrigeration Air-conditioning Contractors.
Solutions or Products Featured
in This Case Study
Heat pump module chillers with Dry Fog humidification have achieved a 67% reduction in CO2 emissions.
There has been an estimated 67% reduction in CO2 emissions compared to conventional air conditioning systems in the facility where it was installed.
In terms of reducing the use of fossil fuels, such as heavy oil, the combination of heat pump module chillers and the Dry Fog humidification system has emerged as a significant success story for our company in lowering environmental impact and achieving energy savings.
The design, including the heat pumps, was arranged by SANSHA ELECTRIC.
Seeking alternatives to the use of steam boilers that consume fuel oil and require frequent maintenance.
From the perspectives of maintenance and CO2 reduction, eliminating steam was the primary condition. Over the years, we have frequently encountered several issues, including clogged and blocked water pipes leading to inefficient operations, coil replacements, and pinholes on the pipes causing steam leaks. Additionally, the use of fuel oil, a hazardous substance, further underscored our serious need for an alternative to the steam boilers.
Improving scale issues with DI water and ensuring sufficient space for fog evaporation by installing the humidifiers under the floor.
We repeatedly experienced nozzle clogging due to water scale. However, this time, we have been hopeful that use of RO water for humidifier will improve maintainability.
Because water spray humidification requires a space for the fog to evaporate, we perform it under the floor. Additionally, the air in cleanrooms circulates through HEPA filters, which should prevent the detection of particles derived from the underfloor humidification. However, we conducted spray tests before implementation to ensure there were no issues and to avoid any quality problems.
Humidifier with least maintenance: it’s been extremely beneficial for us on-site.
It has been running for a full five years with virtually no troubles, which has been extremely beneficial for us on-site. Using RO water for humidifier, we have avoided problems such as clogged nozzles that prevent the fog from spraying.
Having experienced it firsthand, it has turned into conviction.
Dry fog humidification allows for humidity control in each independent zone, enabling us to set the system to closely match the targeted humidity.
Initially, we aimed to regulate humidity within the cleanrooms to a targeted level of approximately 45% RH, with a variation of +/-10 to 15%. Steam was supplied to the rooms using the dew point control method at the outside air handling unit. However, due to temperature variations among the different cleanrooms, it is suspected that certain rooms may have experienced higher humidity levels than the targeted 45%.
Dry fog humidification, which allows for dividing the cleanrooms into zones for individual control, enables us to adjust the humidity in each zone separately to the targeted 45%, with a variation of approximately 2–3%.
Indirect humidification under the cleanroom floor using Dry Fog
Eager to implement any improvements related to energy for carbon neutrality.
In the past, the air handling units commonly relied on boilers for humidification. However, Dry Fog humidification has emerged as a superior alternative, providing precise humidity control on a zone-by-zone basis while only humidifying as needed. Additionally, this system offers substantial cost savings compared to the expense of upgrading the boiler.
As part of our company-wide goal towards carbon neutrality, we are committed to undertaking any energy-related improvements moving forward.