Dual-Function Single Nozzle for Cleaning-In-Place (CIP) in Aseptic Filling Machines
Technical Library
- HOME
- Technical Library
- Chemical-Resistant Tank Cleaning Nozzle with Anti-Detachment Mechanism for CIP
Chemical-Resistant Tank Cleaning Nozzle with Anti-Detachment Mechanism for CIP

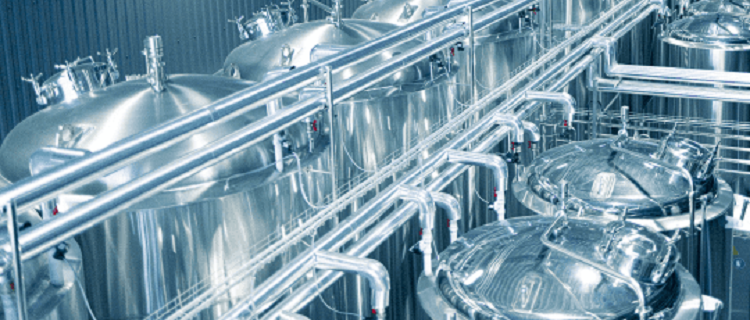
Note: The product used in this case is a custom version of the ESV-PTFE Series, as detailed in the following article.
Solutions or Products Featured
in This Case Study
Key Reasons for Implementation
- Proposed a mechanism to prevent Teflon nozzles from falling off in high-temperature environments.
- Offered a solution to prevent static electricity generation and the resulting risk of ignition.
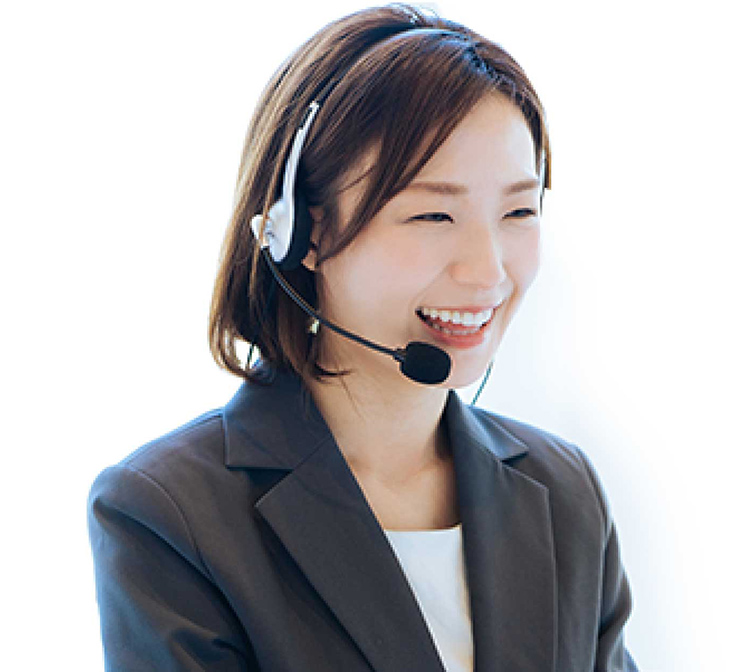
- Not sure which product is right for you?
- Curious about the total cost?
- Wondering where to start?
- We’re here to help – reach out with any questions.
Challenges Faced by the Customer
A tank manufacturer serving chemical processing plants contacted IKEUCHI, inquiring about the design and production of a 3D rotating nozzle for Clean-In-Place (CIP) systems, tailored for integration with their tanks.
This tank is used in chemical processing and requires nozzles made of chemical-resistant Teflon.
The CIP cleaning process for this tank is as follows: first, the interior is rinsed with ultrapure water after chemical processing, followed by drying with steam and hot air. The ultrapure water is at room temperature, while the internal temperature during drying reaches 170°C.
However, since the maximum operating temperature for Teflon nozzles is 93°C, there were concerns that the threads could expand and loosen during the drying process, risking the nozzle falling off.
A solution to minimize this risk was needed.
Proposals from IKEUCHI
To ensure the proper operation of the nozzle, altering the specified operating temperature was not an option. As an alternative, a double-nut structure was devised.
This involves attaching and tightening a nut on the liquid supply piping side (connecting adaptor, part #1 shown below), while also threading the hub (part #3) and securing another nut there.
This design is expected to prevent the nozzle body or the entire nozzle from falling off, even if slight loosening occurs.
Additionally, to reduce the risk of ignition from static electricity generated by ultrapure water, we proposed using Teflon filled with carbon graphite as a conductive material.
Benefits Achieved
Three years have passed since the nozzle installation, and no issues such as falling off or ignition have occurred. The user’s facility continues to operate reliably, ensuring stable chemical production to this day.