Suppressing Airborne Dust at a Coal Storage Facility with Ultra-Fine Fog
Technical Library
- HOME
- Technical Library
- Dust Suppression at Blast Furnace Tapholes Using High-Velocity, High-Volume Fog
Dust Suppression at Blast Furnace Tapholes Using High-Velocity, High-Volume Fog
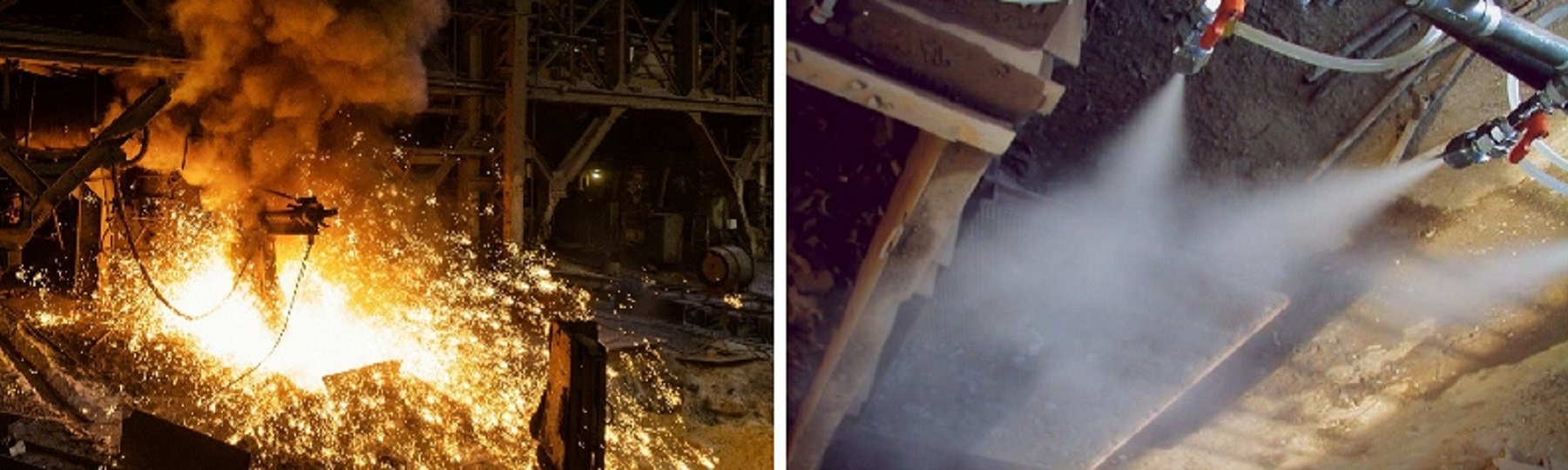
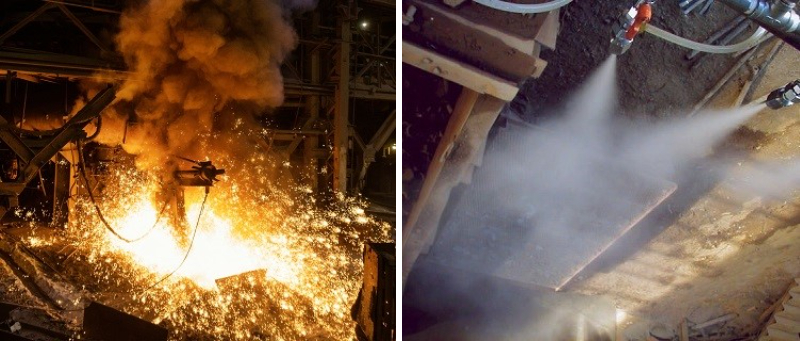
Solutions or Products Featured
in This Case Study
Dust Control at Steel Plants
Steelmaking involves multiple processes that are prone to significant dust emissions, particularly at raw material yards, coke ovens, and blast furnace tapholes, where the risk of airborne dust dispersion is especially high.
Dust stirred up in such areas can remain suspended in the air and spread beyond the site boundaries, leading to complaints from nearby residents and serious concerns over deteriorating workplace conditions at the plant. In fact, the need for countermeasures continues to grow as such cases persist.
At outdoor raw material yards, dust dispersion has traditionally been mitigated through water sprinkling and dust suppression nets, while coke ovens are typically equipped with dust collectors—each area employing countermeasures tailored to its specific conditions.
Remaining Challenges Around the Blast Furnace Taphole
In contrast, dust generated at the blast furnace taphole has proven difficult to fully contain, leaving workplace environment improvement an ongoing challenge.
Around the blast furnace taphole
The primary sources of airborne dust are twofold: the taphole and the main runner, which channels the molten iron.
At the taphole, airborne dust is generated when the molten iron comes into contact with air. To address this, a dust collection hood is installed above the observation window used to monitor tapping operations, capturing airborne dust at the source.
The molten iron then flows through the main runner to the next process. A cover approximately 8 meters long is installed over the runner to prevent splashing of molten iron and to suppress the dispersion of airborne dust.
However, during the taphole opening operation, the main runner cover must be temporarily moved to avoid interference with the taphole drilling machine.
Main runner cover temporarily removed to avoid interference with taphole drill
Taphole opening with a drilling machine
Dust erupts as the taphole is opened
During the 3–4 minutes of taphole drilling, the main runner remains uncovered, allowing the dust to ride rising hot air currents and spread throughout the building.
Dust rides rising hot air currents and spreads throughout the building
Solutions Proposed by IKEUCHI
To address this issue, IKEUCHI proposed a dust suppression system that sprays high-volume, high-velocity fog to prevent dust from erupting into the air and spreading throughout the facility.
By installing multiple nozzles diagonally above the taphole and spraying toward the taphole area, the system suppresses dust at the source and prevents it from rising with the thermal updraft and spreading throughout the facility.
With its fine droplet size, the fog does not wet nearby floors or equipment.
Eliminating the need for large-scale installation work, the system can be quickly deployed with only water and compressed air supplied.
Benefits Achieved
Delivering high-velocity, high-volume fog, the system effectively covers dust-emission points without being displaced by rising hot air, significantly reducing dust dispersion. As a result, working conditions around the blast furnace taphole have improved, along with overall site safety.
IKEUCHI’s fog continues to contribute to maintaining safe, secure working environments and mitigating dust-related pollution.
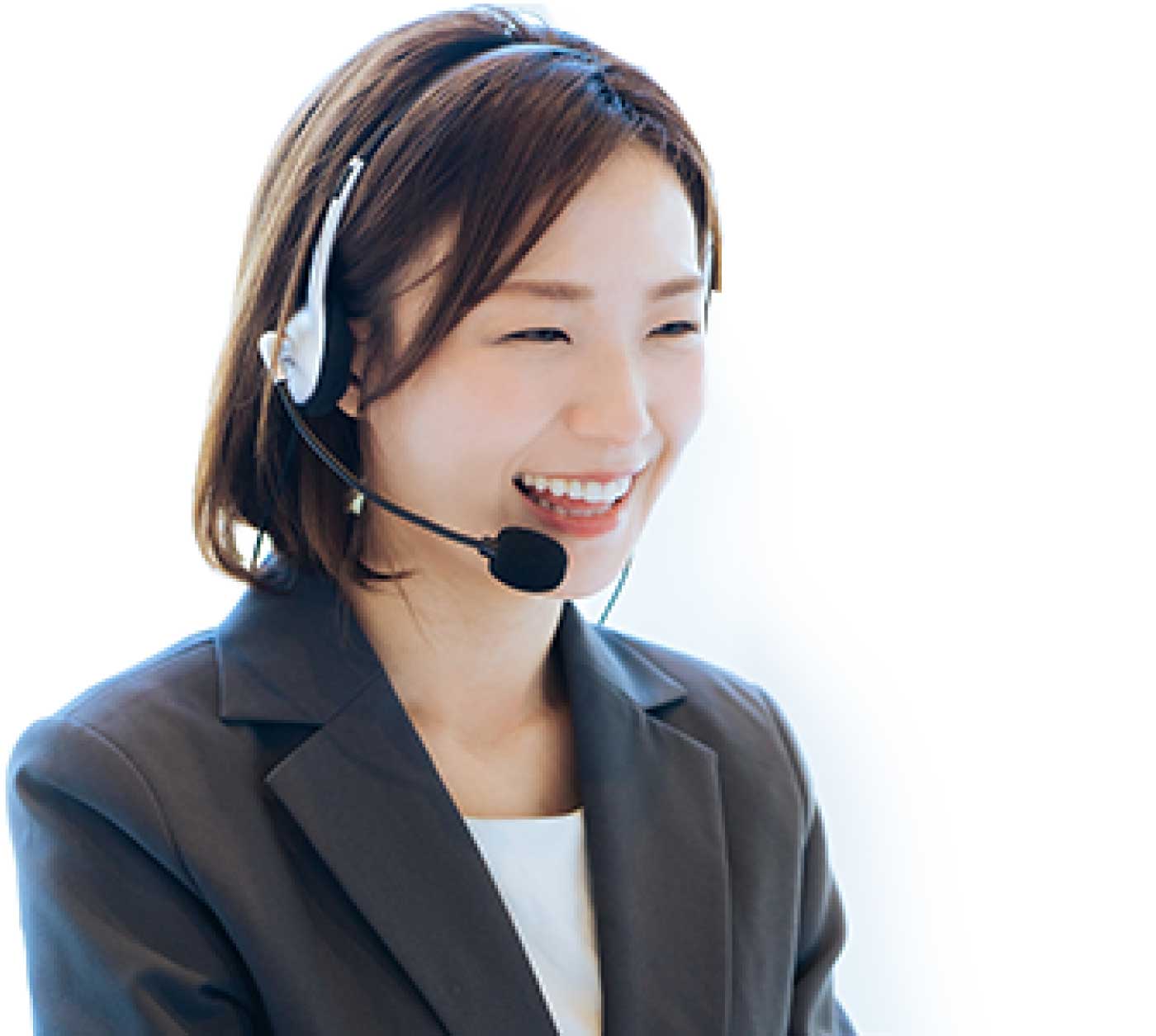
- Not sure which product is right for you?
- Curious about the total cost?
- Wondering where to start?
- We’re here to help – reach out with any questions.