Technical Library
- HOME
- Technical Library
- Particle Board Factory | Jet Auto Backwash Strainer Reduces Release Agent Disposal Costs by 80%
Particle Board Factory | Jet Auto Backwash Strainer Reduces Release Agent Disposal Costs by 80%
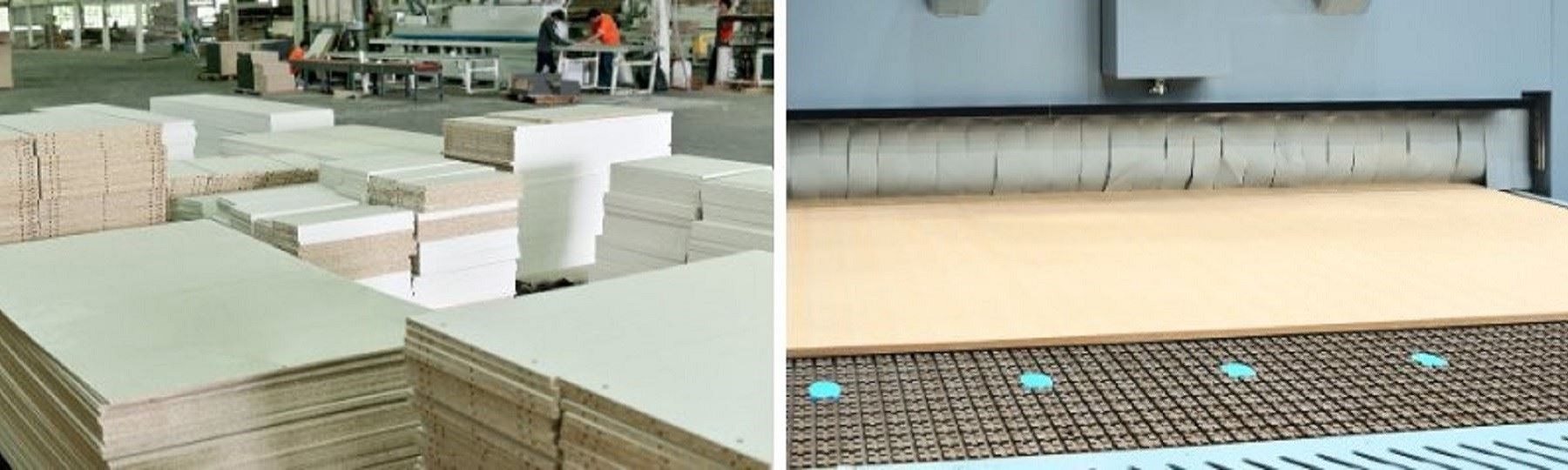
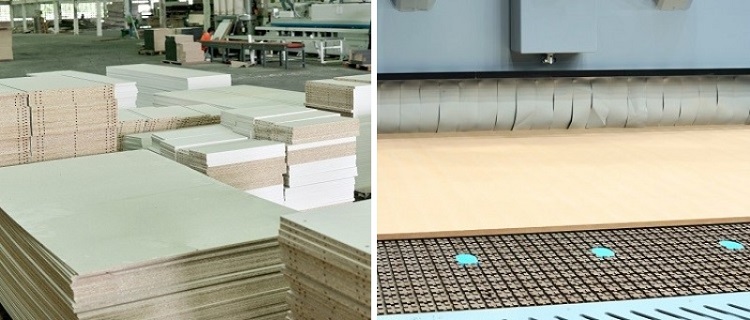
Solutions or Products Featured
in This Case Study
Key Reasons for Implementation
The following benefits were confirmed through testing with a demonstration unit:
- Eliminates the need for manual filter cleaning.
- Effectively removes wood chips from the release agent liquid to enable waste liquid reuse.
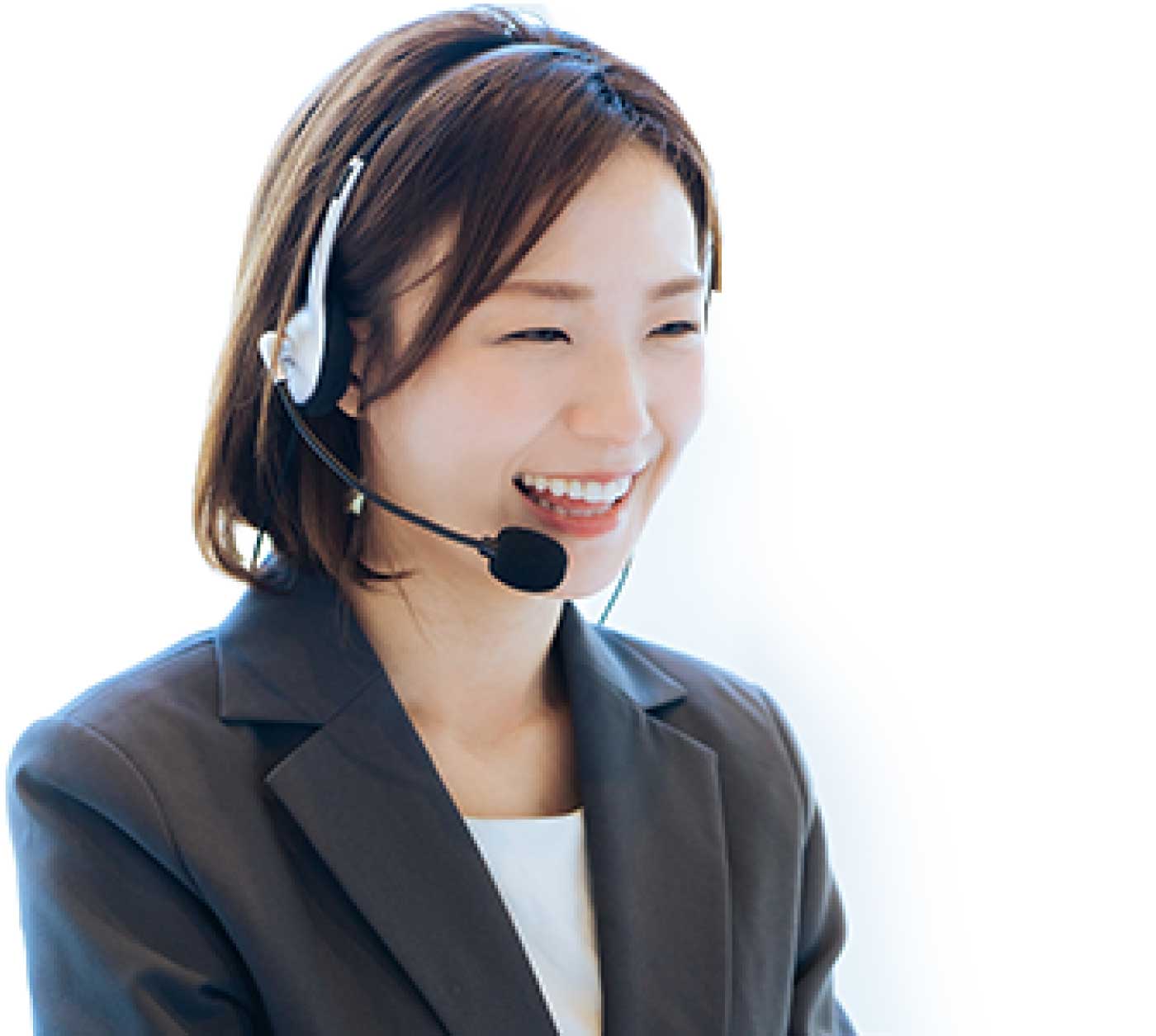
- Not sure which product is right for you?
- Curious about the total cost?
- Wondering where to start?
- We’re here to help – reach out with any questions.
Challenges Faced by the Customer
A particle board manufacturing factory was spraying a release agent onto the boards after shaping the material mixed with adhesive to prevent them from sticking to the conveyor. However, the associated costs had become a significant burden, prompting them to initiate a cost-reduction project.
Particle board transport on conveyor after forming
Spraying release agent
They were consuming 1m³ of the release agent per day, which translates to more than 2 liters per minute during 8 hours of operation. The disposal of waste liquid after spraying incurred an annual cost of 7 to 8 million yen.
Additionally, before disposing of the waste liquid, they had to manually clean the filters used to remove wood chips from the liquid three times a day.
To drive the project forward, the customer sought our support to address the following challenges:
- Reduce the waste liquid volume by collecting and reusing it.
- Lower the overall consumption of the release agent through reuse.
- Eliminate the need for manual filter cleaning.
- Avoid clogging of the release-agent spray nozzles with wood chips, which could hinder the spraying performance.
Proposals from IKEUCHI
We proposed the automatic backwash strainer ARS Series.
Automatic Backwash Strainer ARS Series
This automatic strainer detects the differential pressure between the supply liquid inlet and the filtered liquid outlet caused by foreign object buildup on the screen during filtration and automatically activates backwashing.
Next, spray nozzles positioned inside the screen emit jet streams, effectively removing foreign objects that have accumulated on the outside.
The removed foreign objects are discharged through the drain outlet, and the liquid supply and the filtration processes automatically resume. This cycle ensures that the strainer effectively maintains its functionality while achieving fully automated operation.
An on-site test promptly conducted with a demonstration unit confirmed its effectiveness.
Filter Screen Before Foreign Object Removal (Left) and After Automatic Backwashing with Jet Spray (Right)
Building a system with this unit enables the filtration of wood chips from the sprayed release agent liquid and the recirculation of the liquid for reuse.
Benefits Achieved
Effectively removing wood chips from the release agent liquid resulted in an 80% reduction in the annual waste liquid disposal costs, which previously amounted to 7–8 million yen. Simultaneously, the consumption of the release agent liquid was also reduced by 80%.
Additionally, eliminating the need for manual filter cleaning freed operators to focus on other tasks, significantly improving overall efficiency.