Spray Nozzles for Food and Beverage Processing | 10 Case Studies (Part 1)
Technical Library
- HOME
- Technical Library
- Automating Fermentation Tank Cleaning with 3D Rotating Nozzles to Solve Labor Shortages
Automating Fermentation Tank Cleaning with 3D Rotating Nozzles to Solve Labor Shortages
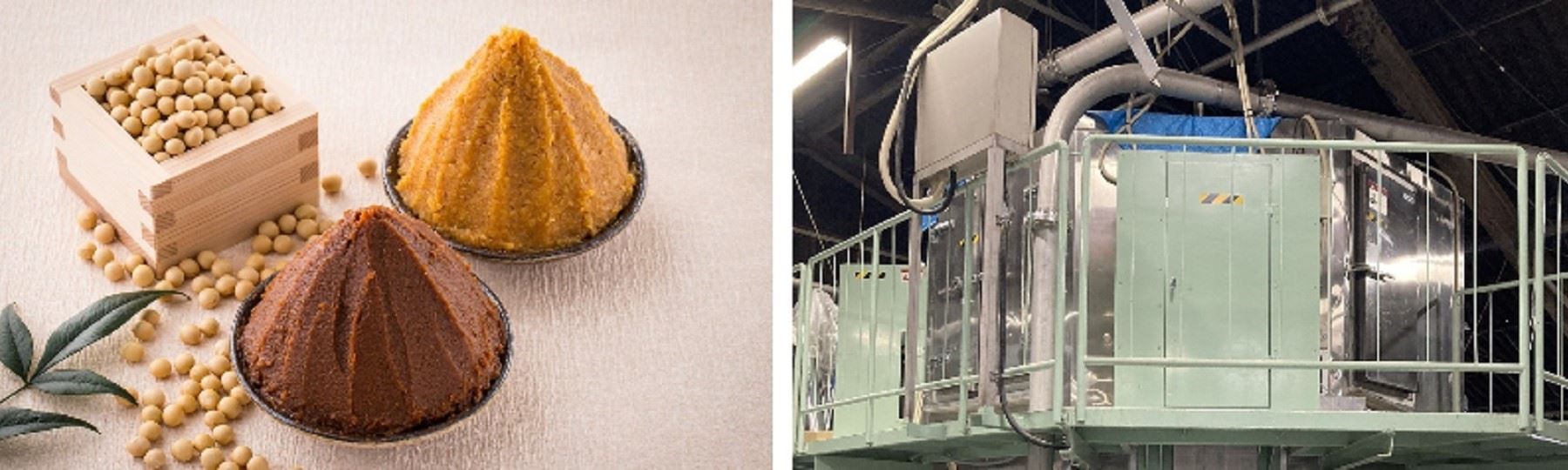
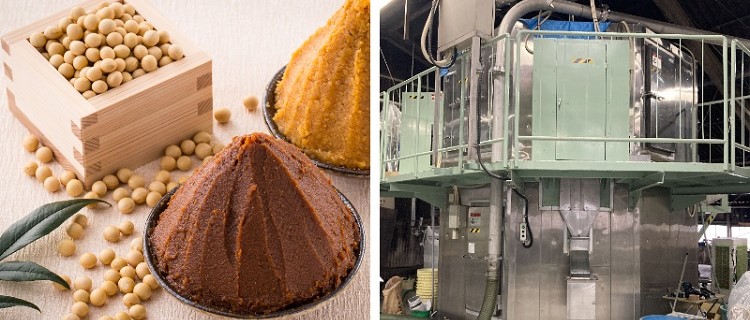
Solutions or Products Featured
in This Case Study
Key Reasons for Implementation
- The selected 3-dimensional rotating tank cleaning nozzle enabled automated cleaning.
- Testing on actual equipment demonstrated its high cleaning efficiency and confirmed its effectiveness in addressing labor shortages.
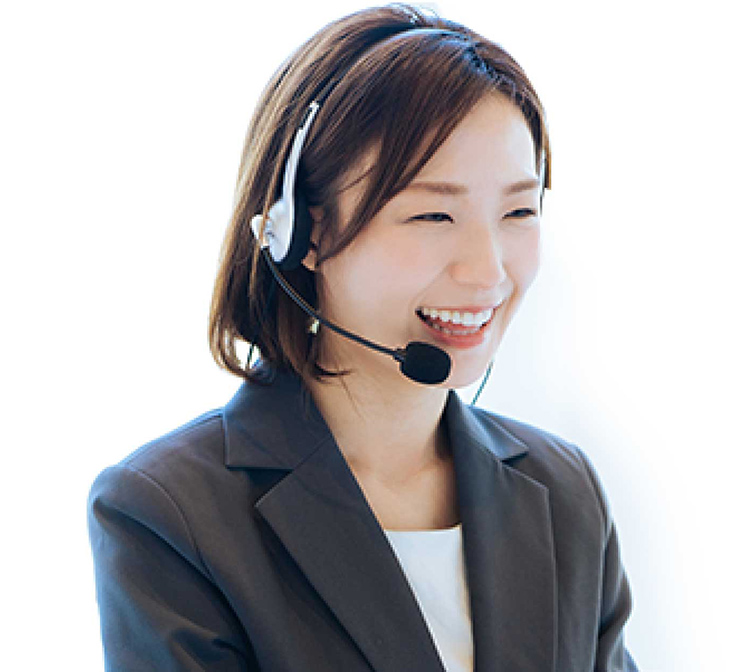
- Not sure which product is right for you?
- Curious about the total cost?
- Wondering where to start?
- We’re here to help – reach out with any questions.
Challenges Faced by the Customer
At Kanemitsu Miso in Fuchu City, Hiroshima, Japan, operators were manually cleaned fermentation tanks used in the rice malt production process. The company’s organic, additive-free miso has earned an excellent reputation, with demand surging particularly in overseas markets. Exports now account for 90% of total sales, and rising orders have made labor shortages a pressing issue.
The fermentation tanks, measuring 3.5 meters in diameter and 4 meters in height, required cleaning every two to three days. Operators connected tap water to a high-pressure washer and manually cleaned the tanks, a process that took approximately two hours per tank. The customer sought to reduce cleaning time and reallocate labor to other tasks as a solution to address labor shortages.
Proposals from IKEUCHI
After reviewing the operational requirements and conducting an on-site survey, we selected a 3D rotating nozzle with specifications tailored to the available utilities and proposed the optimal installation position. Additionally, we performed on-site testing using a sample unit, confirming that the cleaning performance met expectations.
![]() |
|
Fermentation tank before nozzle installation | Fermentation tank after nozzle installation |
Benefits Achieved
- The manual cleaning process, which used to take two hours, was replaced with automated cleaning, reducing the time to 10–20 minutes and easing the workload. This also helped address labor shortages.
- By using the 3D rotating nozzle, the tank’s inner walls can now be thoroughly cleaned in all directions (360°), leaving only minimal final finishing work to be completed.
- The ability to use hot water has enabled effective removal of protein residues and eliminated lingering odors.