Revolutionizing Direct Mail Printing with Dry Fog Humidification
Technical Library
- HOME
- Technical Library
- Revolutionizing Gravure Printing Processes: Safe and Energy-Efficient Humidification Solutions
Revolutionizing Gravure Printing Processes: Safe and Energy-Efficient Humidification Solutions
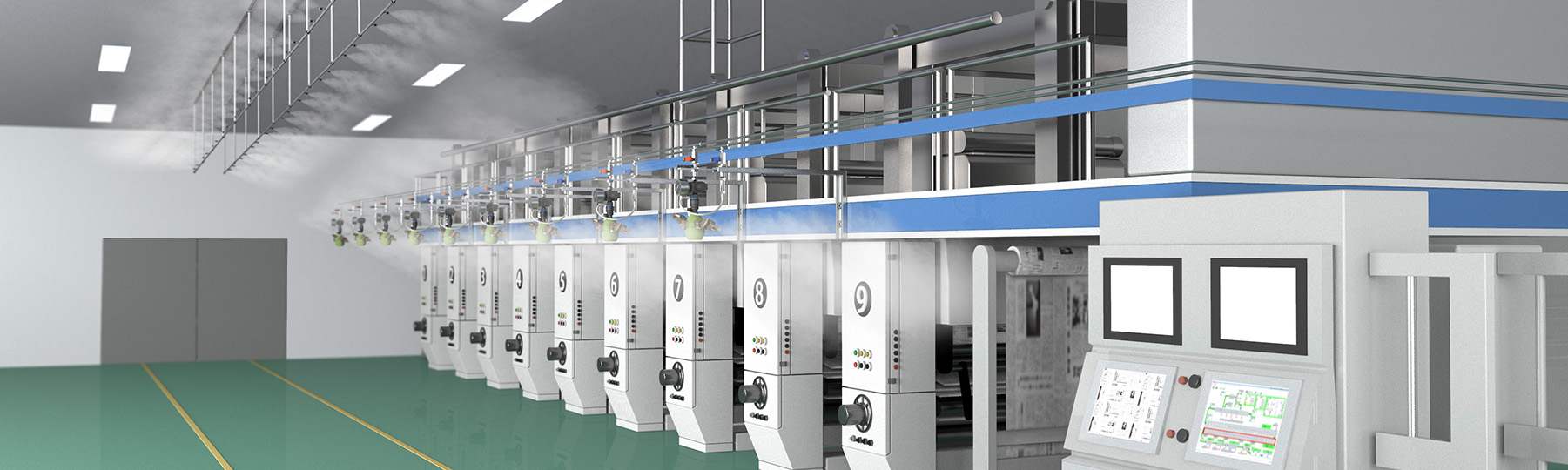
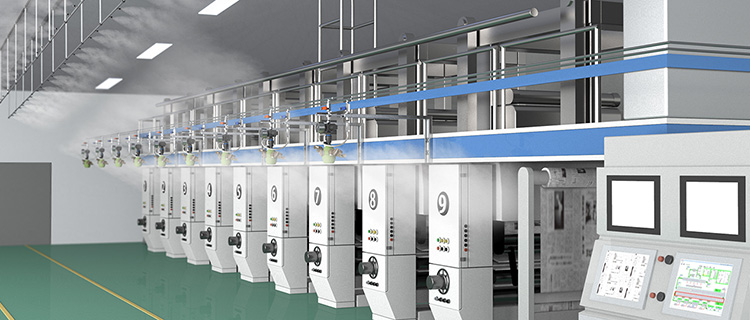
Solutions or Products Featured
in This Case Study
Reasons for Implementation
・The rising costs of electricity and fuel highlighted the benefits of investing in switching humidification methods.
・The demonstration convinced the customer of the feasibility of implementation.
・The high return on investment facilitated seamless budget acquisition.
Challenges at a Gravure Printing Factory
The inks used in gravure printing processes contain highly volatile and flammable organic solvents, which are harmful when evaporated, thereby requiring a large volume of ventilation to refresh indoor air.
On the other hand, ventilation that takes in outside air makes the indoor air dry, especially in winter, increasing the risk of fire caused by sparks from static electricity built up in the process. Furthermore, the dryness can cause airborne dust and particulates to adhere to the products, leading to quality failures. To address these issues, effective humidification equipment is essential in gravure printing factories.
Customer’s Initial Setup and Challenges
The customer who contacted us for solutions to these challenges had a boiler-based steam humidifier system already installed at their worksite. However, in their efforts to reduce CO2 emissions, they were facing issues with the steam humidification, which requires heat for its operation, leading to high fuel and electricity consumption and increased CO2 emissions. Additionally, the recent rise in electricity and fuel costs has become a significant concern.
Switching from boiler-based steam humidification to other methods for energy savings.
Innovative Proposal from IKEUCHI
Switching from the steam humidification to the water spray humidification we proposed required maintaining a relative humidity of 50% around the ink units, where sparks tend to arise.
To achieve this, we selected the AirULM, which was expected to deliver the highest energy-saving performance under the given conditions, from our three system products—AirHybrid, AirAKI, and AirULM—and then proposed the “spot humidification” approach by installing the explosion-proof AirULM headers at positions close to the ink units.
Cost-Effective Spot Humidification
Spot humidification allows for humidity increases at targeted spots, significantly suppressing operating costs compared to the approach of maintaining stable humidity levels across the entire floor.
Customized Installation for Optimal Results
We tailored the header to the length of the printing process line, installing eight nozzles on a 4-meter header. This setup achieved the target condition with approximately one-third to one-half of the total humidification volume required for the entire floor.
Furthermore, by conducting an on-site demonstration, we provided the customer with a hands-on experience, helping them visualize the implementation and understand the cost-effectiveness beforehand.
The nozzle used with the AU header producing a very fine fog with a mean droplet diameter of 20 to 30 µm.
Benefits of Implementation
Halting the use of the boiler-based steam humidification has resulted in substantial energy savings, allowing the initial investment to be recouped in about one year.
The steam humidification, which also caused the worksite temperature to rise, posed a significant burden on the employees working in uniform. However, with the new system, they have reported that it became cooler, and the worksite environment has improved.
Ensuring Safety and Promoting Sustainability
Switching from the steam humidification to the water spray not only ensures safety by reducing fire risks associated with organic solvents and static electricity but also promotes environmental friendliness and energy savings, furthermore contributing to establishing a more comfortable working environment.
Commitment to Continuous Improvement
IKEUCHI remains committed to addressing on-site challenges in printing factories.