Preventing Static Electricity with Humidification: A Guide | Anti-Static Solutions | Industrial ESD Prevention | ESD Elimination with Humidity
Technical Library
- HOME
- Technical Library
- Article by Industry: Electronics | ESD Prevention with Dry Fog | Optimal SMT Manufacturing Environment
Article by Industry: Electronics | ESD Prevention with Dry Fog | Optimal SMT Manufacturing Environment
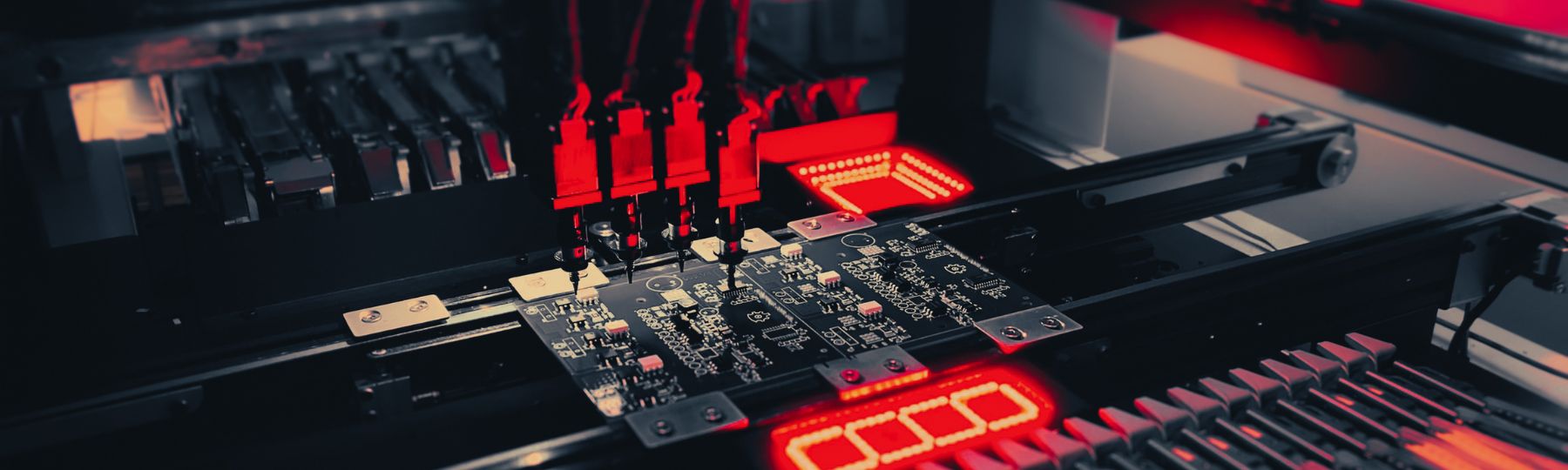
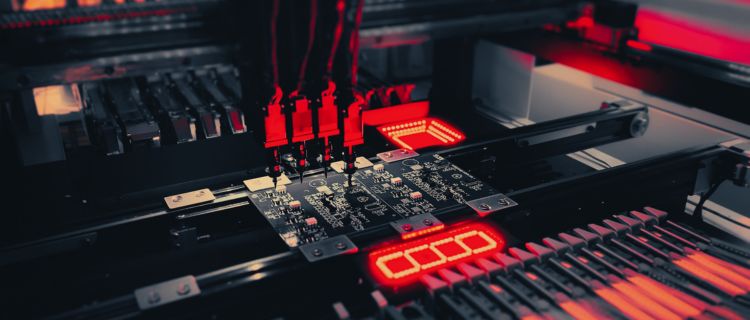
Intro
In the realm of modern electronics manufacturing, Surface Mount Technology (SMT) has revolutionized the production of electronic assemblies, offering efficiency, precision, and miniaturization. SMT involves the intricate process of placing surface mount components onto printed circuit boards (PCBs), a crucial step in creating electronic devices. Central to this process is the utilization of quality nozzles and a precise humidification system. Quality nozzles are fundamental in the wet process. Meanwhile, a well-controlled humidification system plays a pivotal role in the assembly process. This maintains an optimal environment within the manufacturing facility, safeguarding sensitive electronic components from static electricity and preventing issues such as component misalignment or damage due to electrostatic discharge (ESD). In this context, understanding the significance of employing superior nozzles and an effective humidification system is paramount for achieving high-quality, reliable electronic products in SMT manufacturing.
Applications
Where/Who?
- PCB manufacturers
- Semi-conductor manufacturers
- Wet process machine manufacturers
- EMS (Electronic Manufacturing Services)
- HDD (Hard Disc Drive) manufacturers
- Automotive wiring manufacturers
What/Why?
Humidification for assembly process- Surface Mount Technology (SMT) is a method used in the electronics industry to assemble electronic circuits. See below image of steps.
Some issues faced in SMT manufacturing with a lack of humidity, are soldering defects, circuit damage, bad mounts, dust adhesion, etc. AKIMist® E is a complete dry fog humidification system that delivers optimal humidification levels for your facility to prevent these complications and increase efficiency & productivity.
Nozzles for the wet process- the wet process refers to the stages within the assembly process where solder paste is applied, and components are placed.
- Polishing- involves planarizing/leveling the copper surface of the PCB which helps to remove any irregularities or excess copper from the board. This ensures that the copper traces & pads are precisely defined according to design specifications. We recommend our nozzles for wear-resistance:UVVP Series, VP Series, VEP Series
- Developing- this stage involves applying a photosensitive material (photoresist) to the PCB and exposing it to UV light through a mask. The UV light acts to remove the unexposed photoresist which then reveals the patterned areas that need to be etched or where the copper needs to be retained. Our nozzles for precision developing:INJJX Series, JJXP Series, SSXP Series, LYYP Series, YYP Series
- Etching- selectively removes unwanted copper from the PCB using a chemical solution. The exposed copper is dissolved, leaving behind the circuit traces & pads according to the design. Our easy maintenance nozzles for high-efficient fine etching:INJJX-Y Series, JJXP Series, SSXP Series, JJRP Series, INVVEA Series
- Stripping- following etching, the remaining photoresist is stripped from the PCB, leaving behind the finished copper traces & pads. This prepares the board for further processes like solder mask application and component assembly. Our high chemical-resistance nozzles:INJJX Series, AJP-PPS Series, INVV Series, VVP Series
- Cleaning- critical step to ensure PCB surface is free from impurities, which could otherwise interfere with subsequent manufacturing steps or affect the electrical performance of the board. Our precise cleaning nozzles:INJJX Series, JJXP Series, INVV Series, VVP Series, AJP Series, YYP Series, BIM Series, VVEA Series, PSN Series
- Blow-Off Drying- this step follows the cleaning process to remove any excess water or cleaning solution from the surface. This prevents any water-induced defects or issues during subsequent processing steps. Our TAIFUJet® Series air nozzles for powerful, efficient blow-off drying.
AKIMist®E Features Summarized
- Water humidification system with no threat of wetting materials and equipment
- Prevents static electricity in facilities
- Easy installation: Add to existing HVAC
- Adaptable to any layout
- Humidifies AND cools
- Reduces product loss during production
- Improves product quality
- Low maintenance
Access the Ikeuchi USA LinkedIn Newsletter Article Here: Article by Industry: Electronics
- Not sure which product is right for you?
- Curious about the total cost?
- Wondering where to start?
- We’re here to help – reach out with any questions.
- Developing- this stage involves applying a photosensitive material (photoresist) to the PCB and exposing it to UV light through a mask. The UV light acts to remove the unexposed photoresist which then reveals the patterned areas that need to be etched or where the copper needs to be retained. Our nozzles for precision developing:INJJX Series, JJXP Series, SSXP Series, LYYP Series, YYP Series