[事例]耐摩耗材質への切り替えで過酷環境下で使用されるノズルの長寿命化を実現|メンテナンス・保守の軽減
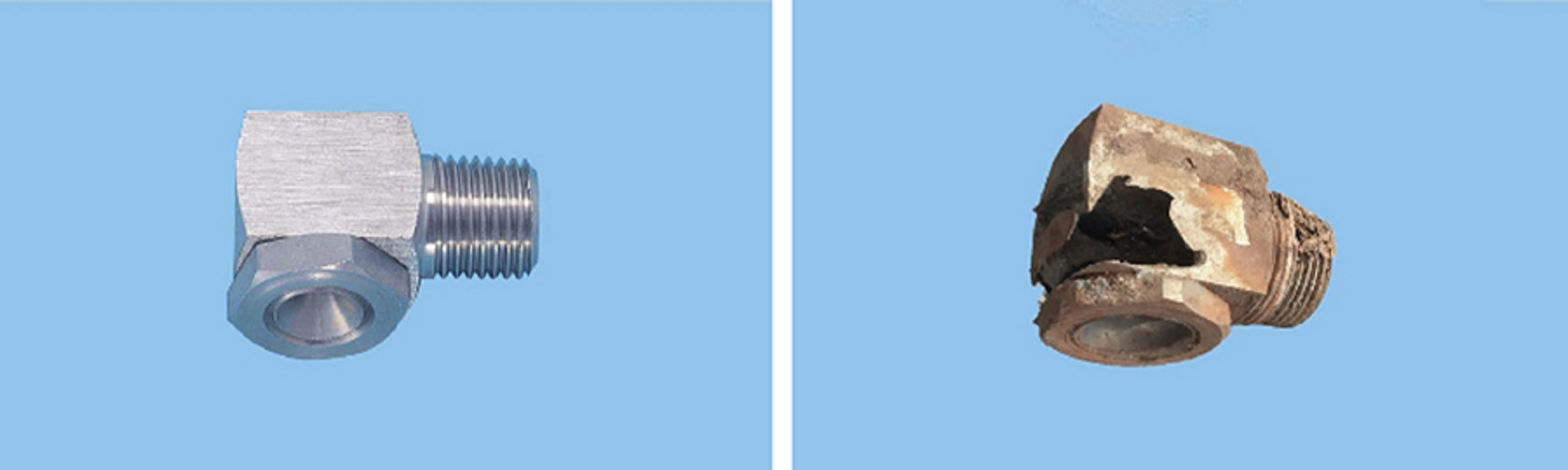
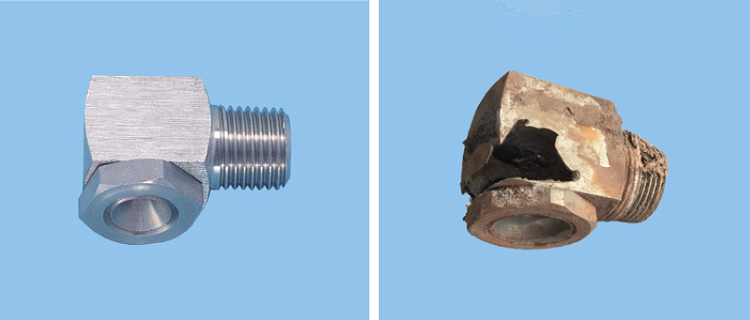
耐摩耗材質への切り替えで過酷環境下で使用されるノズルを長寿命化
本記事では、耐摩耗性に優れた材質を用いたノズルへの切り替えにより、ノズルの長寿命化を実現した事例をご紹介します。
事例1
この事例で使われている製品・ソリューション
導入の決め手
- 耐摩耗性に優れた材質を用いたスプレーノズルへの切り替えにより、長寿命化を実現。
- 劣悪な環境下でも使用可能なノズルを選定。
- 使用開始から3ヶ月経過後も、外観・性能に大きな劣化が見られなかったことが確認されたこと。
お客様の課題
ある製鉄所の焼結工場では、ドラムミキサー内でスラリー液を噴霧するスプレーノズルの著しい摩耗に悩まされていました。
焼結鉱の材料である鉄鉱石、粉コークス、石灰は、焼結機に投入される前にドラムミキサーで混合され、焼結に適したサイズにまで造粒処理されます。その際、造粒性を高めるためにスラリー液をスプレーノズルで噴霧します。
しかし、スラリー液に含まれる粉状酸化鉄がノズルを摩耗させ、新品に交換してからわずか300時間(約1ヶ月)でノズルがボロボロに損傷し、正常に噴霧できなくなるという問題が発生していました。
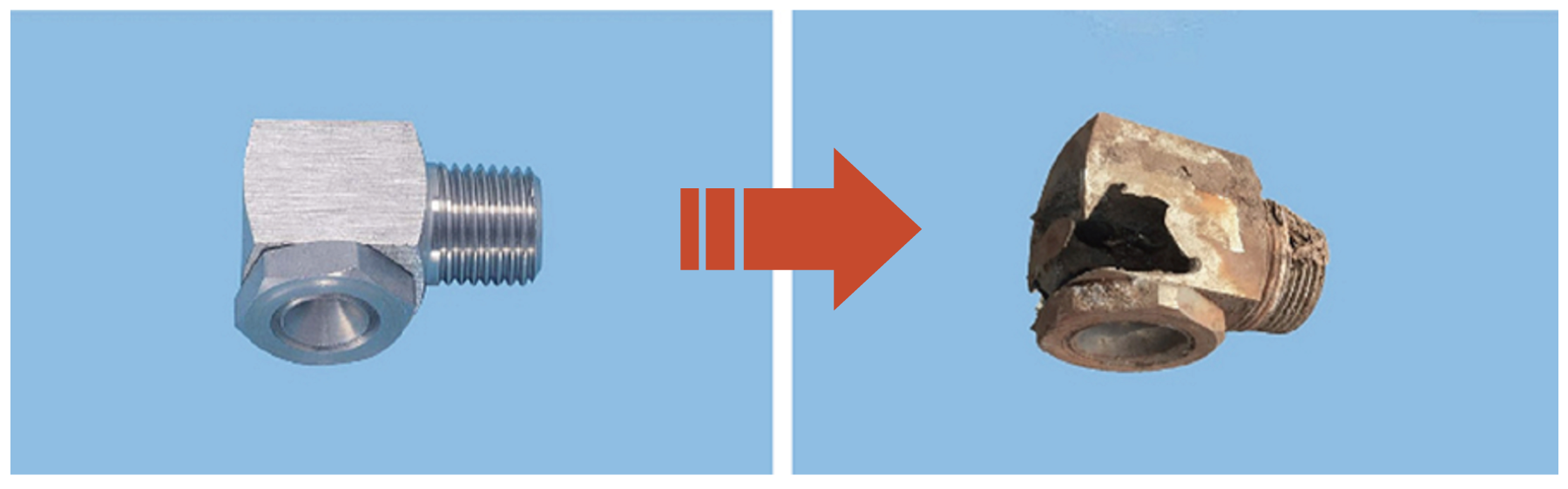
その結果、ドラムミキサーの運転を毎月停止しノズルを交換せざるを得ず、メンテナンス・保守の負担が非常に大きくなっていました。そこで、劣悪な環境下でも長寿命を維持できるスプレーノズルを求め、当社にご相談いただきました。
いけうちからのご提案
従来使用されていたノズルはステンレス鋼SUS303製でした。そこで、同じ性能を維持しつつ、SUS303よりもはるかに耐摩耗性に優れたアルミナセラミック製(アルミナ純度92%)のノズル「AJP-AL92」への切り替えを提案しました。
導入効果
AJP-AL92への交換を早速実施し、使用開始から150時間後に中間検査を行ったところ、ノズルの外観・性能ともに劣化は見られませんでした。その後、3ヶ月後の最終検査でも外観・性能に大きな変化はなく、ノズル寿命が従来の3倍以上に延びたことが確認されました。これにより、メンテナンス・保守の負荷を大幅に軽減することに成功しました。
事例2
この事例で使われている製品・ソリューション
導入の決め手
- 耐摩耗性に優れた材質を用いたスプレーノズルを製作し、長寿命化を実現。
お客様の課題
ある鋳型成形装置メーカー様では、装置内部で砂が舞う環境下でスプレーノズルを使い、離型剤を噴霧する設計を採用していました。しかし、ノズルの損耗が大きな課題となっていました。砂がノズルチップに衝突し続けた結果、わずか半年でボロボロに損傷し、安定した離型剤の噴霧が困難な状況に陥っていたのです。
このままでは装置ユーザーが安定した操業を続けることができません。メーカー様は劣悪な環境下でも長寿命を維持できるスプレーノズルを求め、当社にご相談いただきました。
いけうちからのご提案
ご使用中のノズルの材質はステンレス鋼SUS303で、その硬度はHRB90(HRC硬度11に相当)でした。そこで、硬度HRC58を持つSUS440C(焼き入れ鋼)を材質として使用したノズルの製作を提案しました。
導入効果
SUS440C製ノズルに切り替えた結果、新品への交換後1年が経過しても、離型剤の噴霧に支障をきたすほどの損傷は見られませんでした。これにより、装置ユーザーが安定した操業を続けられる装置が完成しました。