Spray Nozzles Cut Sanitizer Consumption by 70% in Seafood Processing
Technical Library
- HOME
- Technical Library
- Solving Challenges in SNCR | Clog-Resistant Spray Nozzles for Efficient NOx Reduction
Solving Challenges in SNCR | Clog-Resistant Spray Nozzles for Efficient NOx Reduction
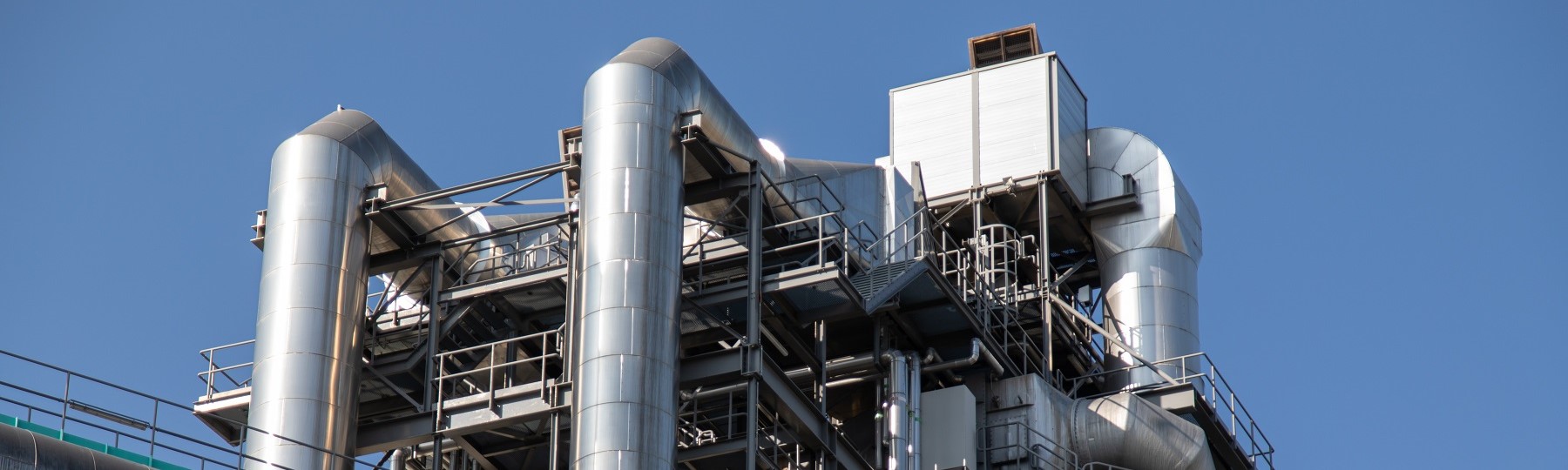
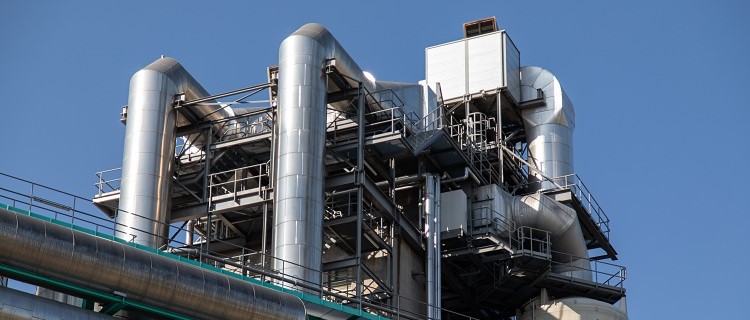
Solutions or Products Featured
in This Case Study
Key Reasons for Implementation
- Selected a clog-resistant nozzle with excellent atomization performance, ideal for urea solution spraying.
- Illustrated the absence of coarse droplets with a flow rate diagram, building customer confidence.
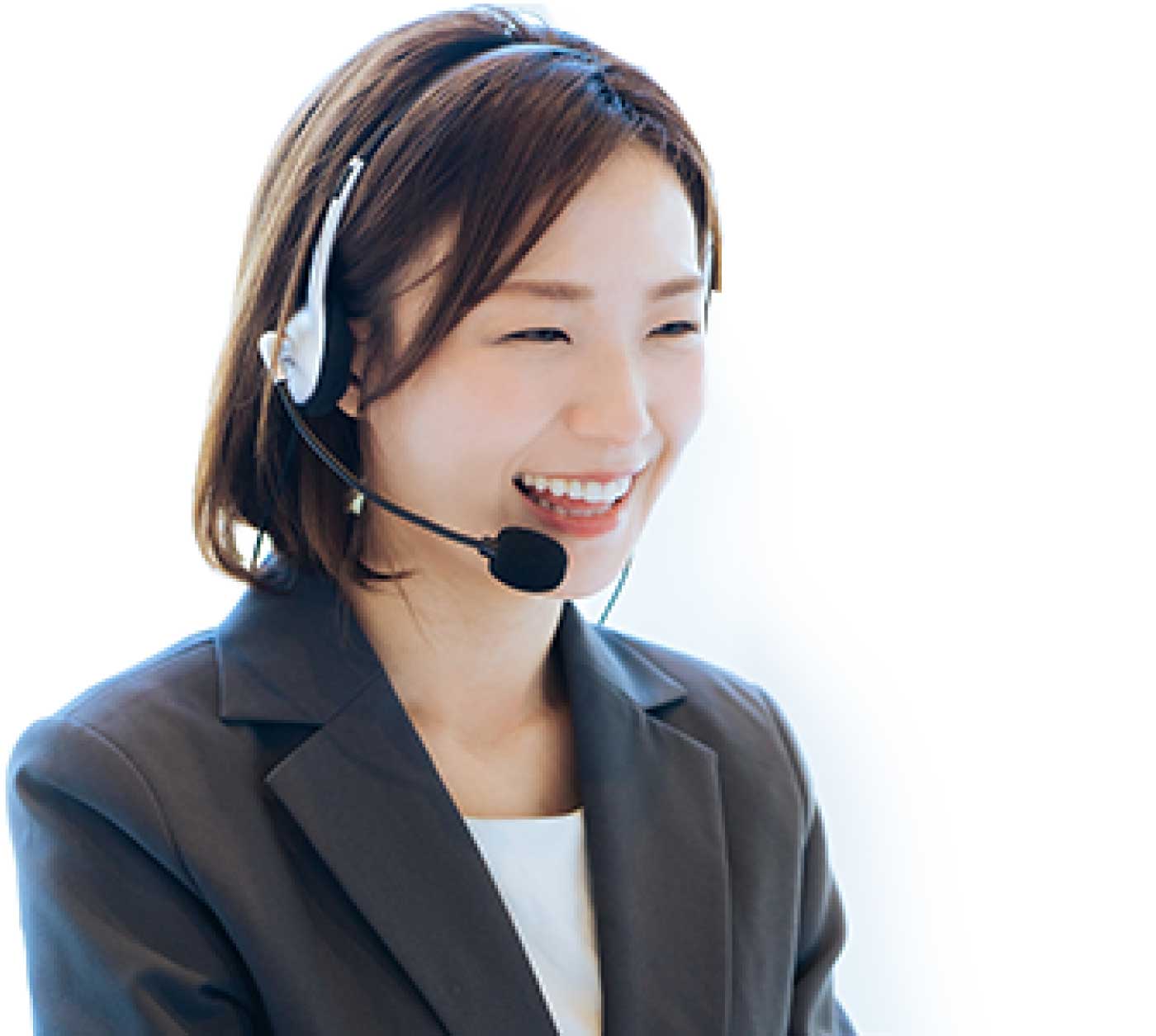
- Not sure which product is right for you?
- Curious about the total cost?
- Wondering where to start?
- We’re here to help – reach out with any questions.
Challenges Faced by the Customer
At a carbon material manufacturing plant, self-procured nozzles were used to spray steam and urea solution into exhaust gases for Selective Non-Catalytic Reduction (SNCR)*.
*Selective Non-Catalytic Reduction (SNCR): a process designed to prevent air pollution caused by nitrogen oxides (NOx) by spraying a reducing agent, such as urea solution or ammonia gas, directly into an incinerator without using a catalyst to chemically reduce nitrogen oxides (NOx) to nitrogen (N2) and water (H2O).
However, the nozzles they used at the time produced spray droplets with uneven sizes, causing non-evaporated coarse droplets to adhere to the inner walls of the incinerator. This caused corrosion of refractory materials, such as bricks and mortar. Furthermore, nozzle clogging caused by urea crystallization was also a recurring problem. To resolve these challenges, the plant consulted us for a solution.
Proposals from IKEUCHI
- Proposed the SETOJet-R Series, an external mixing type that is clog-resistant and delivers excellent atomization performance, as the optimal choice for urea solution spraying.
- Using the nozzle’s flow rate diagram, we effectively demonstrated the absence of coarse droplets, ensuring the customer’s confidence in the benefits of complete evaporation of the urea solution within the furnace—which reduces adhesion to and corrosion of the inner walls while optimizing the reduction efficiency of nitrogen oxides (NOx).
- Presented our extensive track record in similar applications for plant engineering companies, providing reassurance to the customer.
Benefits Achieved
First, a test conducted in one of the furnaces demonstrated improvements in the corrosion of bricks and mortar. Additionally, urea solution consumption was reduced by 40%, yielding an annual cost benefit of US$10,000. Furthermore, complete evaporation eliminated drainage, allowing for the efficient use of urea without waste.
Subsequently, based on these results, the implementation of the solution was considered for other furnaces, and a 90-degree bent-type nozzle was also newly adopted.