Optimizing Coffee Creamer Cup Disinfection to Significantly Reduce Defects
Technical Library
- HOME
- Technical Library
- How Moisture Conditioning Reduced Cream Puff Dough Crack Defects by 80% without Over-Wetting
How Moisture Conditioning Reduced Cream Puff Dough Crack Defects by 80% without Over-Wetting
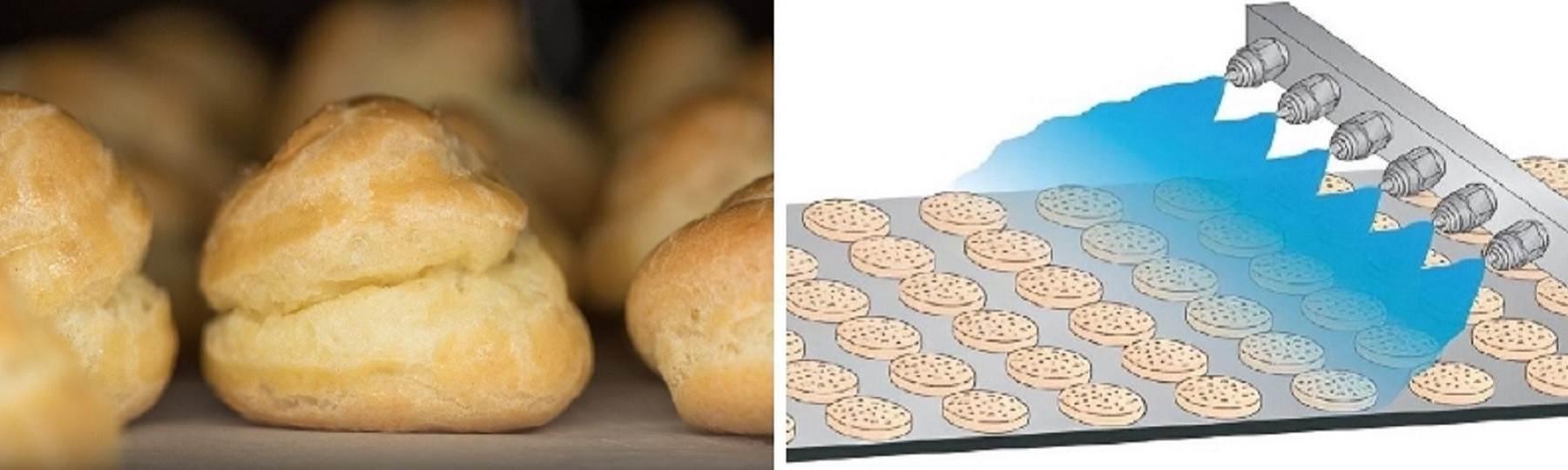
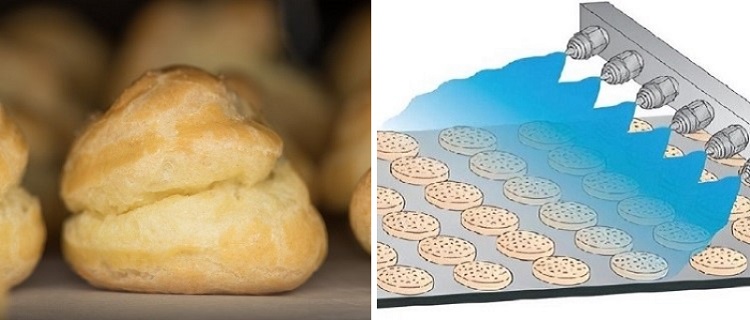
Solutions or Products Featured
in This Case Study
Key Reasons for Implementation
- Proposing an optimal spray nozzle and installation layout tailored to the properties of the dough enabled effective moisture conditioning.
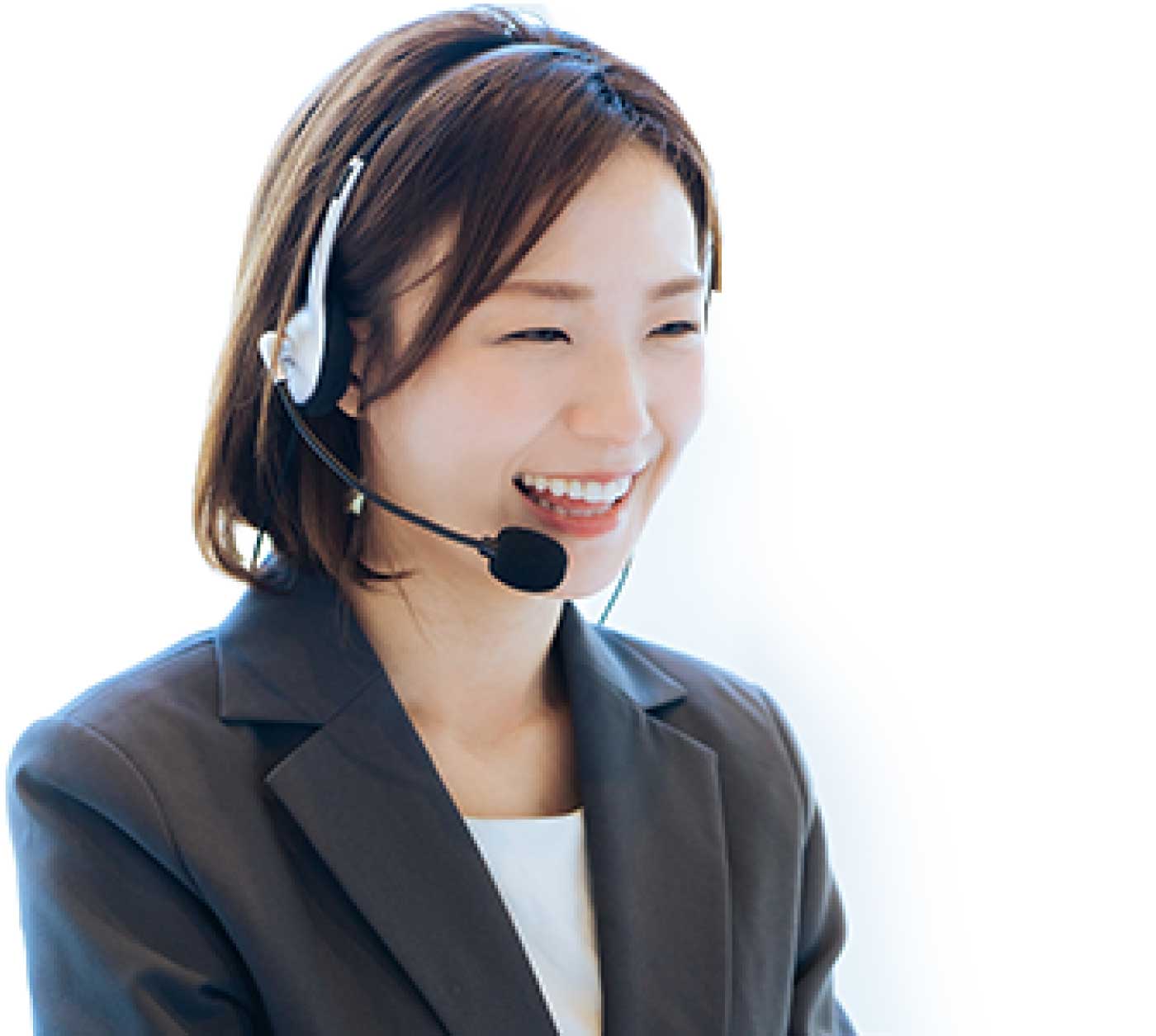
- Not sure which product is right for you?
- Curious about the total cost?
- Wondering where to start?
- We’re here to help – reach out with any questions.
Challenges Faced by the Customer
A confectionery factory was seeking a way to prevent cracks from forming on the surface of cream puff dough during baking. To address this issue, they began exploring methods of moisture conditioning the dough before feeding it into the tunnel oven.
The primary cause of cracking was identified as dryness during baking. While increasing the moisture content of the dough could help prevent cracking, uncontrolled moisture adjustment would negatively affect the final texture.
To tackle this, the customer approached IKEUCHI for a solution to adjust the moisture level of the dough on the conveyor line just prior to baking.
Proposals from IKEUCHI
IKEUCHI selected the BIMJ pneumatic spray nozzle, which sprays a minimal amount of moisture evenly across the dough surface in the form of an ultra-fine fog. This nozzle enables ideal droplet formation that lightly moistens the surface without over-wetting.
We created a spray unit that can uniformly cover the entire width of the conveyor by installing multiple BIMJ nozzles onto a Food Sanitation Act-compliant nozzle header prepared by the customer.
Note: The nozzle parts used complies with the Food Sanitation Act in Japan. Please either prepare a compliant nozzle header on your end or contact your IKEUCHI sales representative for assistance.
Benefits Achieved
The solution successfully reduced the defect rate by 80%, significantly decreasing product waste.
Future Development
IKEUCHI is currently working on the basic design of a portable automatic spray control unit. The unit will combine a nozzle header with a cart-mounted spray control panel and pressurized tank for flexible deployment.
By simply supplying power and compressed air, the unit can be positioned alongside existing production lines to enable flexible spray operation. The goal is to complete a product that requires no installation work or piping, making implementation quick and easy.
Note: For food-processing applications, ensure that any surface of our product that may come into contact with your products or processes complies with applicable food safety regulations and standards.