[インタビュー]宇部興産 宇部セメント工場|ロータリーキルンシェルをミストで冷却、煉瓦損耗と維持補修費を低減
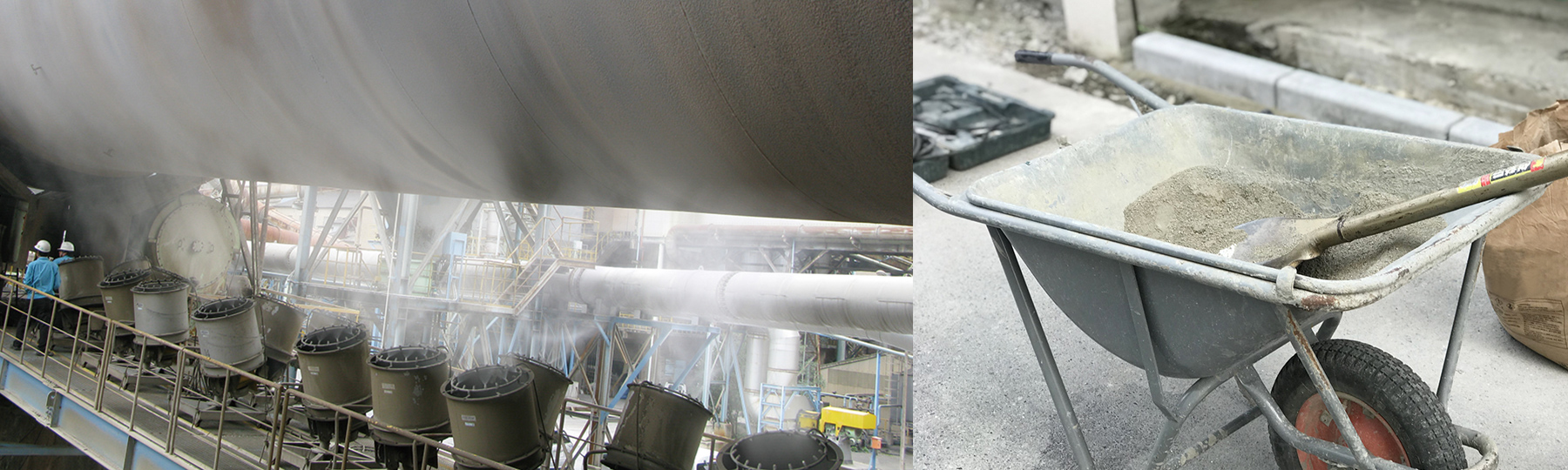
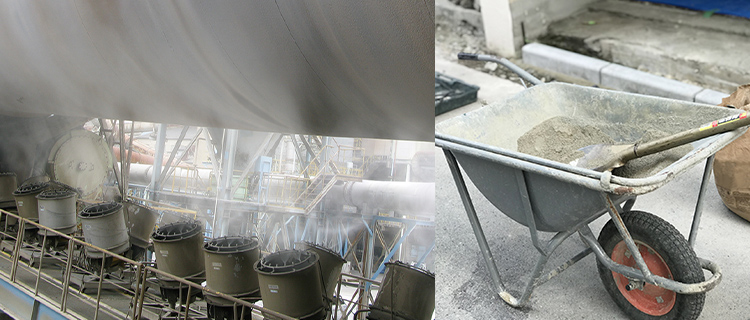
企業情報
セメントの生産は年間180万t、普通ポルトランドセメントのほか、早強ポルトランドセメント・高炉セメントなどの
特殊セメントを約50種類生産可能で、多様化・高度化したニーズに対応する製品を社会に提供されています。
キルン微霧冷却システムをいけうちとともに開発いただき、その特許を取得されています。
この事例で使われている
ソリューション・製品
廃棄物利用がキルン負荷に
当社は、循環型社会の形成に貢献すべく、早くからクリンカ焼成用の熱エネルギー代替として可燃性廃棄物を受け入れ、現在は年間300万t以上の廃棄物・副産物を有効利用しています。
一方で硫黄、塩素を多く含む廃棄物の利用増加は、ロータリーキルン(以下キルン)の煉瓦内の組織結合を破壊し、溶損を早めるといった新たな問題を生みました。
増大するキルン維持補修費
キルンの劣化損傷を早める原因は廃棄物利用の増加だけでなく、キルン冷却が原因の場合もあります。
例えば当工場で長らく用いてきた空冷式の冷却。これはエアーが当たる狭い範囲しか冷やせません。全体的に冷却不足に陥ることが多く、コーティング・煉瓦の溶損や脱落が発生することがあり、表面鉄皮(以下シェル)の熱変形が懸念されました。
当社伊佐セメント工場では水冷式を用いていましたが、冷えすぎることでシェルと煉瓦の間に酸結露が発生し、シェルを内側からじわじわと腐食させてしまうことがありました。またこの方式はシェル表面の温度計測ができないので、たとえキルン内部で異常が発生していても見つけることができません。
廃棄物利用の増加、従来的な冷却によりやむを得ず発生する損耗、原因は多数ありますが、キルンを含む設備の維持補修費は数年で約7倍にも膨れ上がっていました。
対策の糸口は「霧」
維持補修費削減のためには、シェルの温度分布を可視化し、適切な温度コントロールによるトラブルの回避、早期対応ができる冷却システムが必要でした。
糸口として上がったのは「霧」を用いたキルン冷却。手法自体は以前からありましたが、いかんせん霧のボリュームが少なくキルン全体を冷却できない、ノズルの目詰まりが多発するといったデメリットを聞き及んでいました。
ただ、温度計測を阻害せずシェルの温度分布の可視化ができる、完全蒸発するので環境や周辺設備に影響を与えない、水冷式と比べ使用水量を大幅に低減できるなど、霧を用いた冷却には多くのメリットがあります。
例えば、複数のノズルを配した大型ファンから従来より多くの噴霧と送風を行いキルン全体を冷却可能にする、フレキシブルな温度コントロールのため部分的に霧の量や風量を増減可能にする、ファン自体もキルンに沿って動かせるようにする、といったことが実現できれば理想的な冷却手法になり得ます。
論より証拠。早速開発に取りかかることになり、パートナーとして、非常に微細な霧「微霧※」を噴霧できるノズルメーカーいけうちに声をかけました。
※微霧:平均粒子径(霧の平均サイズ)が10~100μmの霧。
24時間 150日 ノーメンテ
システムの概要は、先ほど言ったノズル付きのファン、噴霧制御盤、これには走査型放射温度計からの温度情報をフィードバックさせます。水は工業用水を利用するため、いけうちのフィルター自洗式ろ過装置「ARSフィルター」を使用、各種ポンプ、タンクなどから構成されます。
また24時間150日ノーメンテナンスを設計コンセプトの一つとして、耐久性にもこだわり開発を進めました。
何度かの試作・検討を経て、目詰まり対策、配管やタンクの防錆・防藻対策など、諸々の課題をクリアし、微霧冷却システムが完成したのは、開発開始からおよそ1年後のことです。
異常への早期対応が可能に
完成したキルン微霧冷却システムは伊佐セメント工場に導入し実証データの収集にあたることに。まず分かりやすい改善効果として、冷却不足、過冷却への早期対応が可能になりました。
表面温度が200℃を下回って、酸結露が懸念される箇所は、意図的に噴霧を停止、場合によっては送風も停止して過冷却を防ぎます。
逆に400℃以上の高温箇所が発生した場合は、問題の箇所へ集中的に霧が当たるよう、ファンの位置や噴霧角度を調整し、コーティングの脱落や煉瓦の溶損を抑えます。仮に煉瓦が脱落してしまった場合でも、シェルの熱変形まで進行しないよう対策しながら操業を継続することが可能です。
ノンドレンで環境負荷なし
水冷式ではキルン周辺が水浸しとなり、周辺設備や作業環境に悪影響を与えていましたが、微霧冷却システムでは霧が完全蒸発しドレンが発生しないので、常にクリーンな状態を保てます。
伊佐セメント工場は内陸にあるため、環境負荷を最小限に抑えることができるのはISOの観点からも良い効果だと言えるでしょう。
また使用水量の削減にも大きな効果が表れています。水冷時は6,500ℓ/hの水が必要だったのに対し、微霧冷却では2,400 ℓ/hしか必要としません。
煉瓦の損耗速度低減
補修費削減に繋がる効果も出ています。煉瓦は消耗品ですので、毎日僅かずつですが損耗していきます。キルンの稼働状況によって変わりますが、だいたい1年くらいで巻替工事が必要になるケースが多かったです。
キルン微霧冷却に切り替えてからは煉瓦の損耗速度が緩やかになり、耐用日数がずいぶん延びました。
シェル温度を可視化したことでコーティングの付着状況が把握できるようになったこと、職員の温度コントロールに対する意識が向上したことなどを受け、煉瓦溶損が起きにくい状態を維持できるようになったためです。
10年間ノーメンテナンス
その後、当工場にも微霧冷却システムを導入。少々調整期間はありましたが、以降は10年間ノーメンテナンスで運用を継続しています。
重要なのはイニシャルコストを下げるために、構成機器の耐久性を落とさないことです。防錆・防藻対策、その他メンテナンスフリーに繋がる性能にはしっかりコストをかけて構築することが大事です。費用対効果は十分出ており、かけたコストは必ず回収できますからね。
微細な霧が蒸発する際の気化熱を利用してキルンシェルを冷却
キルン微霧冷却システム
微霧を噴霧し、ロータリーキルンシェルを冷却、一定の温度範囲内に制御することにより物の補修周期を延長(延命)可能なシステムです。
ドレンが発生しないため、周辺環境を汚染することがありません。シミュレーション解析(有償)を行って提案内容を見える化することも可能です。