[事例]グラビア印刷工場|蒸気式加湿からの切替えでCO2 排出量を大幅削減(防爆仕様の加湿設備)
[事例]タイヤ製造|混錬工程・バンバリーミキサー周辺をスポット加湿し静電気発火・引火を防止
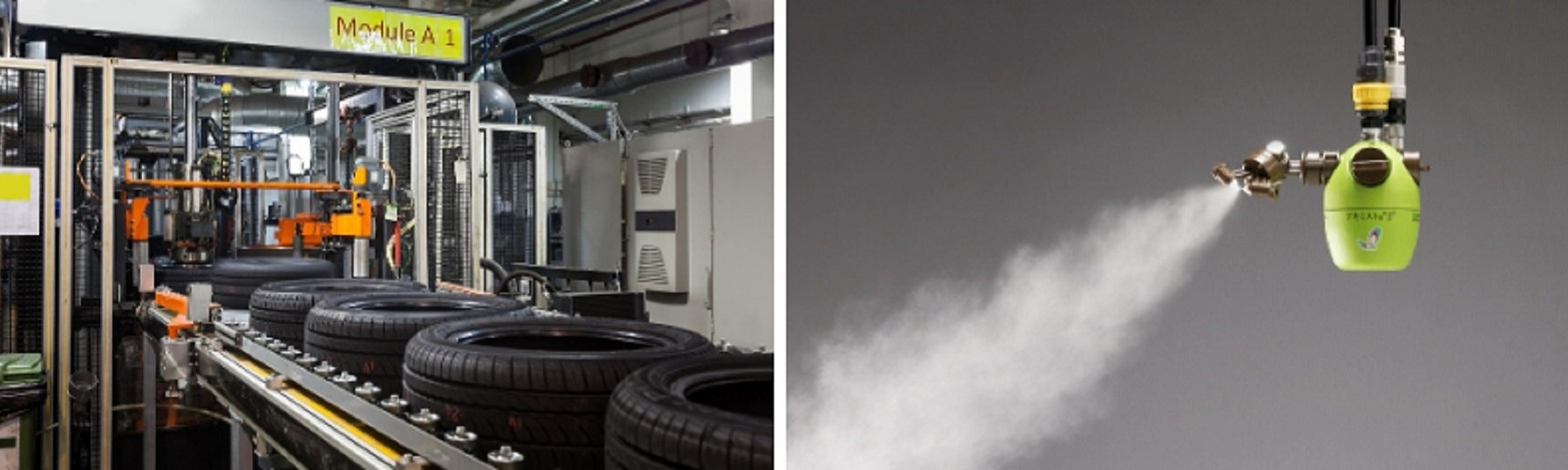
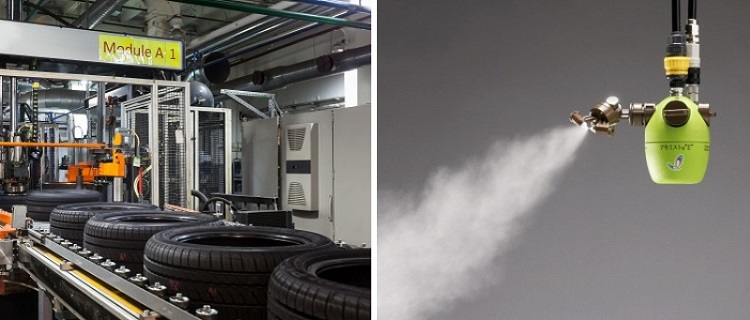
この事例で使われている
ソリューション・製品
導入の決め手
- 課題を抱える特定工程の設備周辺だけを、効果的かつ効率的にスポット加湿できる製品だったこと。
タイヤ製造工程
タイヤは、天然ゴムや合成ゴムにさまざまな配合剤を加えて加工し、複数の工程を経て製造される製品です。その主な工程は以下のとおりです。
- 混錬工程
天然ゴムや合成ゴムに、カーボンブラック、硫黄、シリカなどの配合剤を加え、練り上げます。 - トレッド押出
練り上げたゴムに熱を加えて押し出し、トレッド形状に成形した後、所定の長さに裁断します。 - 成型
トレッドとその他の部品を組み合わせ、タイヤの形を作る工程です。この工程を終えたものを
「生タイヤ」と呼びます。 - 加硫
生タイヤを金型に入れ、熱と圧力を加えることで、トレッドパターン(タイヤの溝)を刻み、最終製品に仕上げます。 - 検査
完成したタイヤの表面を仕上げた後、バランスや均一性、異物混入の有無などを検査して品質を確認します。
混錬工程とバンバリーミキサー
タイヤ製造において、混錬工程は最終品質を左右する重要なプロセスです。
この段階でゴムと配合剤をどれだけ均一に混ぜられるかが、その後のすべての工程に大きく影響します。
この混錬を担うのが、バンバリーミキサー※です。
密閉型チャンバー内でローターが回転し、ゴムに強い力を加えながら練り上げることで、配合剤をムラなく分散させます。
バンバリーミキサー(イメージ画)
こうした混錬作業を安定して高精度で行えることが、バンバリーミキサーの大きな特長です。
※バンバリーミキサー(Banbury Mixer)の名称は、その発明者であるファーンリー・H・バンバリー(Fernley H. Banbury)氏に由来しています。
混錬工程における課題
バンバリーミキサーは高性能で、タイヤ製造工場において欠かせない設備ですが、混錬工程そのものには課題も残されています。
混錬中、チャンバー内では原材料と機械の摩擦に加え、ゴムが強くねじられたり折り返されたりする過程で大量の熱が発生します。
この熱により練ゴムの温度が上昇し、さらに密閉されたチャンバー内に蓄積された熱が装置全体に伝わることで、ミキサー周辺の雰囲気温度も高くなります。
雰囲気温度が高温になると湿度が低下し、乾燥した環境が生まれます。こうした乾燥した状態のもとでは、たとえば周辺にある他の装置の電源部から発生する火花や、静電気によるスパークが硫黄を含む練ゴムに引火し、火災に至るリスクが現実の脅威となっています。
いけうちからのご提案
このような低湿度環境による静電気のスパーク発生や引火リスクを防ぐには、いけうちの「ドライフォグ加湿器 AKIMist-E」を活用した加湿が最適です。
AKIMist-Eに搭載された専用ノズルが発生させる超微細な霧「ドライフォグ」は、噴霧後すばやく蒸発し、周辺の空気にうるおいを与えます。設備や製品に触れても濡らすことがなく、ノズル1個あたり毎分2.4リットルの噴霧ができるパワフルな加湿器です。
工場全体を加湿する必要はありません。
バンバリーミキサーを囲むようにAKIMist-Eを数台設置し、その周辺だけをスポット加湿することで、効果的かつ効率的な引火防止対策を実現できます。
導入効果
ドライフォグ加湿器の効果は、すでに多くのタイヤ製造工場で認められています。同じメーカー様内でも、複数工場への導入が着実に広がっています。
いけうちの製品は今日も、確実な防火対策と、安全安心な現場環境の維持に貢献し続けています。