Effective Cooling with Mist Fans for Harsh Working Environments in Explosion-Proof Zones
Technical Library
- HOME
- Technical Library
- Mist Cooling: Reducing Cycle Time and Boosting Productivity in Vehicle Parts Coating
Mist Cooling: Reducing Cycle Time and Boosting Productivity in Vehicle Parts Coating

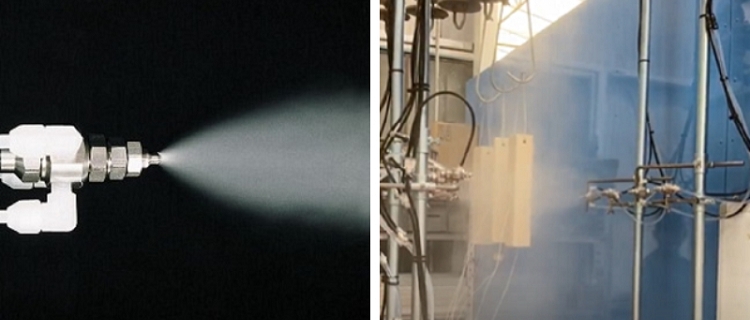
Solutions or Products Featured
in This Case Study
Key Reasons for Implementation
- Mist cooling, without wetting the product, proved to be a highly efficient solution.
- The cooling process time was reduced from 11 hours with natural cooling to just 5 minutes, significantly boosting productivity.
- The proven effectiveness of the cooling process ensured worker safety during subsequent packing and shipping operations.
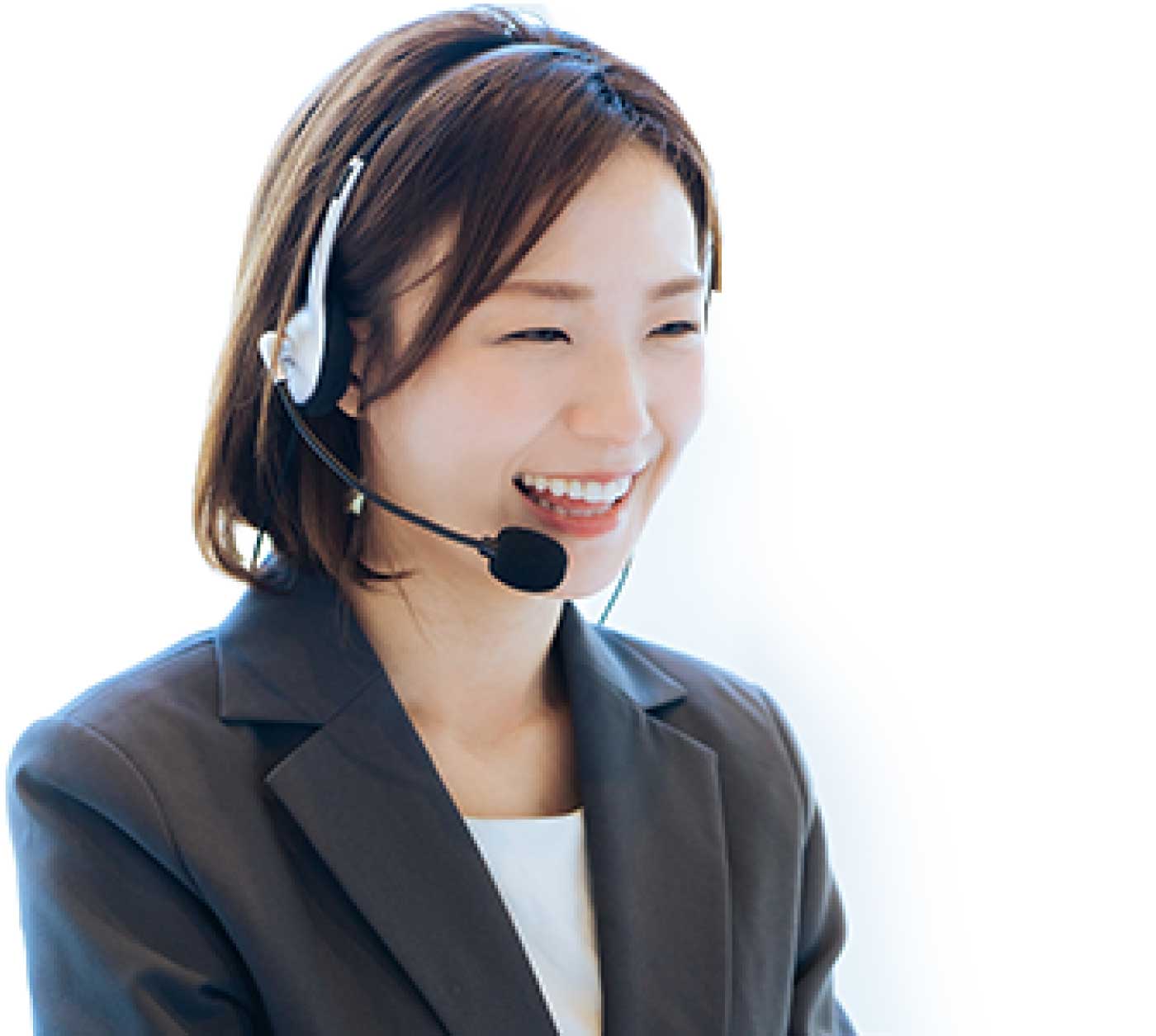
- Not sure which product is right for you?
- Curious about the total cost?
- Wondering where to start?
- We’re here to help – reach out with any questions.
Challenges Faced by the Customer
A coating engineering company was supporting its customer in upgrading the cooling process that follows the coating of vehicle parts.
This process involves curing the products in a drying oven, taking them out, and then cooling them.
To safely handle the products by hand during the subsequent packing and shipping processes, they needed to be cooled down to around 60°C from approximately 190°C.
This customer previously relied on natural cooling for 11 hours before performing packing operations in the morning of the following day.
However, with increasing demand for their products, they faced the need to boost shipment volumes, but their current method could no longer keep up. Forced to address this limitation, they reached out to us for a solution to shorten the cooling time.
Proposals from IKEUCHI
We proposed a method using a pneumatic spray nozzle to cool the products with a fine fog without wetting them. A sample unit was promptly installed on the production line, and testing was carried out in a layout where fog was sprayed onto the products as they were conveyed on hangers from the drying oven.
Benefits Achieved
During the testing, the surface temperature of the products was measured. Temperatures were recorded at six different points on the products, and the resulting temperature change curves are plotted in the graph below.
The findings are as follows:
- The product temperature immediately after exiting the drying oven was approximately 190°C and it dropped to around 65°C within 5 minutes.
- A brief rise in temperature, known as recalescence, was observed at some measurement points, but the temperature decreased to 60°C within an additional 2 minutes, posing no issues.
The test was successful, and the system installation is now underway. With this solution, products can be manually packed just 10 minutes after exiting the drying oven, greatly improving productivity while ensuring worker safety.