Custom-Designed Spray Nozzles for Producing Higher-Quality Carbon Blacks
Technical Library
- HOME
- Technical Library
- Extended Nozzle Lifespan with Wear-Resistant Materials: Reducing Maintenance Burdens
Extended Nozzle Lifespan with Wear-Resistant Materials: Reducing Maintenance Burdens
- Iron & Steel
- Wear-Resistant
- Slurry
- Drum Mixer
- Release Agent
- Hydraulic Spray Nozzles
- Pneumatic Spray Nozzles
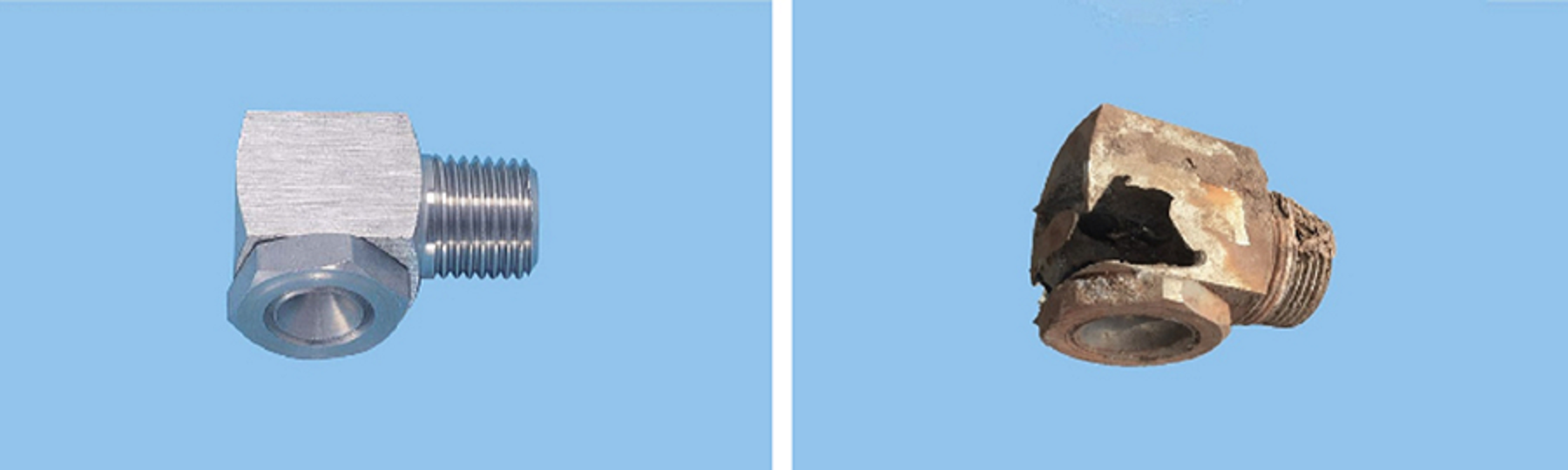
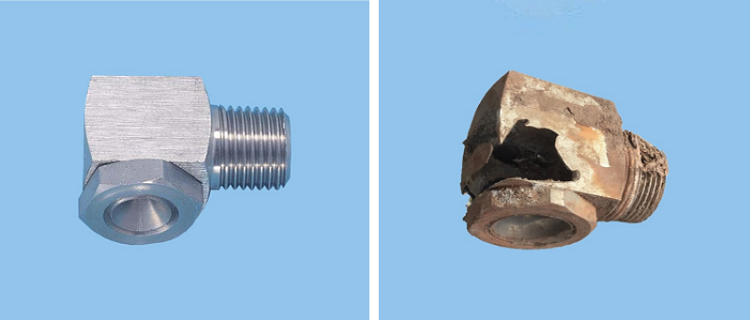
Extending Nozzle Lifespan in Harsh Environments with Wear-Resistant Materials
This article presents two case studies showcasing how switching to nozzles made of highly wear-resistant materials significantly extended their lifespan, even under challenging conditions.
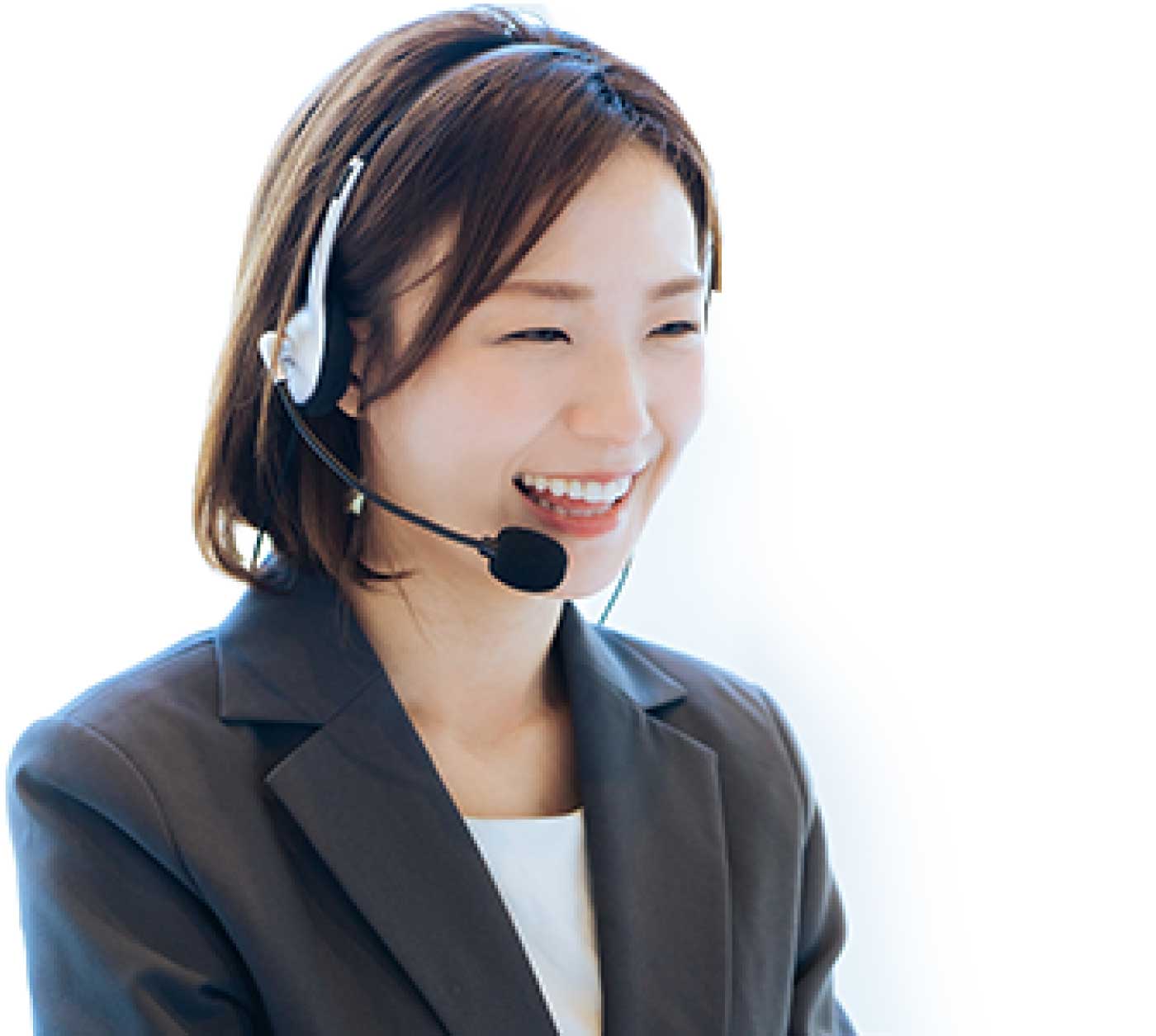
- Not sure which product is right for you?
- Curious about the total cost?
- Wondering where to start?
- We’re here to help – reach out with any questions.
Case Study 1
Solutions or Products Featured in This Case Study
Key Reasons for Implementation
- Switching to spray nozzles made from highly wear-resistant materials achieved an extended lifespan.
- The selected nozzles proved to operate reliably in harsh environments.
- Even after three months of use, the nozzles demonstrated no significant deterioration in appearance or performance.
Challenges Faced by the Customer
At a sintering plant in a steelworks, significant wear on the spray nozzles used for spraying slurry inside the drum mixer had become a major concern.
Iron ore, coke fines, and lime—the raw materials for sintered ore—are mixed in a drum mixer and granulated to a size suitable for sintering before being fed into the sintering machine. During this process, spray nozzles are used to apply slurry, enhancing granulation efficiency.
However, the powdered iron oxide in the slurry caused significant wear on the nozzles. After being replaced with new ones, the nozzles were severely damaged and became unable to spray properly after only 300 hours (about one month) of use.
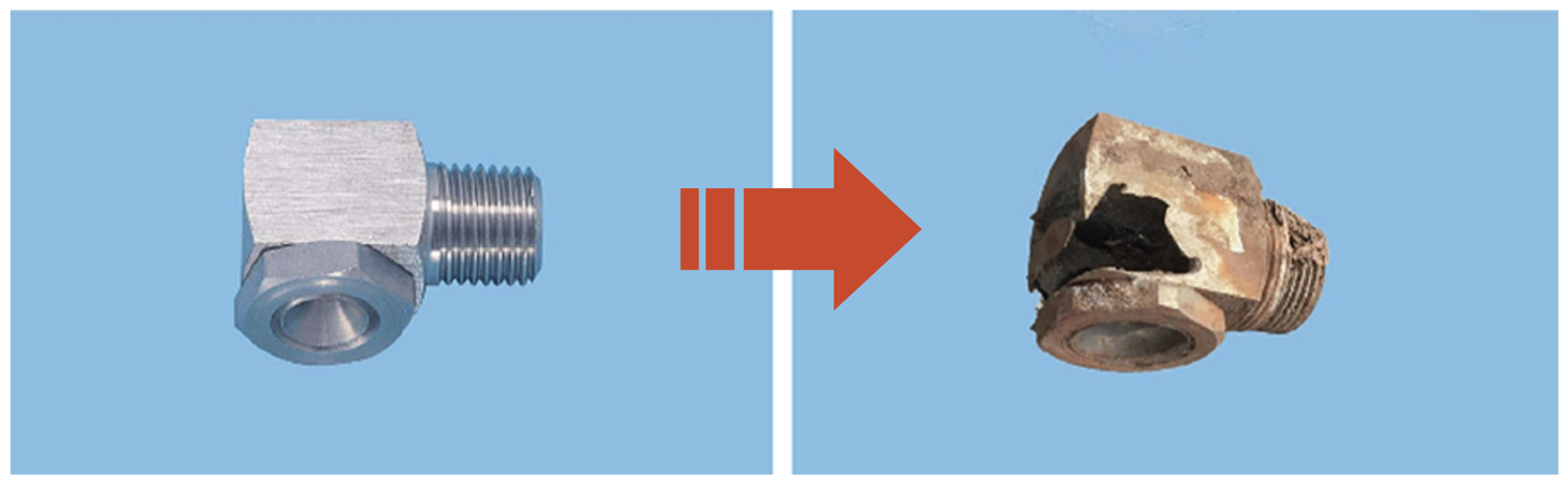
Consequently, the drum mixer had to be shut down every month for nozzle replacement, substantially increasing the burden of maintenance and upkeep. In search of spray nozzles capable of maintaining a long lifespan even in harsh environments, the customer reached out to us for a solution.
Proposals from IKEUCHI
The nozzles previously in use were made of stainless steel 303 (SUS303). To maintain the same performance while greatly enhancing wear resistance, we proposed switching to the AJP-AL92 series, crafted from alumina ceramic with a 92% purity, which offers far superior wear resistance compared to SUS303.
Benefits Achieved
The switch to the AJP-AL92 series was promptly implemented, and an interim inspection conducted after 150 hours of use revealed no signs of deterioration in either the nozzles’ appearance or performance. A final inspection three months later also demonstrated no significant changes in appearance or performance, confirming that the nozzle lifespan had more than tripled compared to the previous model. This resulted in a substantial reduction in maintenance and upkeep burdens.
Case Study 2
Solutions or Products Featured in This Case Study
Key Reasons for Implementation
- Switching to spray nozzles made from highly wear-resistant materials achieved an extended lifespan.
Challenges Faced by the Customer
A sand molding machine manufacturer had adopted a design that utilized spray nozzles to apply release agents in an environment where sand particles circulated inside the equipment. However, nozzle wear became a significant issue. Continuous impacts from the sand particles on the nozzle tips caused severe damage, leaving the nozzles heavily deteriorated within just six months and making it difficult to maintain stable application of the release agents.
This situation made it impossible for machine users to maintain stable operations. The manufacturer sought spray nozzles capable of delivering a long lifespan even in harsh environments and reached out to us for a solution.
Proposals from IKEUCHI
The material of the nozzles in use was stainless steel 303 (SUS303), with a hardness of HRB90 (equivalent to HRC11). In response, we proposed manufacturing nozzles made from stainless steel 440 C (SUS440C), which offers a hardness of HRC58.
Benefits Achieved
As a result of switching to SUS440C nozzles, no significant damage affecting the spraying of release agents was observed even after one year of use following replacement. This ensured that the machine provided users with stable and reliable operation.